User Area
Software Release History - Version 18
New Facilities and Improvements
in LUSAS Version 18.1 and 18.0
Release history
V18.1-2 made available on 5 January 2020
This is an error
fix release to correct an urgent software issue preventing the loading
of any results file generated since midnight 1st January 2021 into
LUSAS Modeller.
Other error fixes and
change requests are included.
V18.1-1 made available on 18 December 2019
This is a minor release
of new facilitites, enhancements and change requests
In summary:
- Time-dependent prestress facilities now support CEB-FIP Model Code 1990 allowing calculation of losses based upon time inputs and calculated stresses.
- The material library now supports the definition of advanced properties for CEB-FIP Model Code 1990.
- The LUSAS Vehicle Load Optimisation facility now supports design code loading to UK bridge assessment code CS 454 Assessment Of Highway Bridges And Structures; Design Manual for Roads and Bridges, Volume 3, Section 4, Part 3, Highways Agency, June 2019.
- The LUSAS Rail Load Optimisation facility now supports design code loading to the United States of America AREMA Manual for Railway Engineering Chapter 8 Concrete Structures (2018 Edition) and AREMA Manual for Railway Engineering Chapter 15 Steel Structures (2018 Edition).
V18.0-6 made available on 5 January 2020
This is an error
fix release to correct an urgent software issue preventing the loading
of any results file generated since midnight 1st January 2021 into
LUSAS Modeller.
Other error fixes and
change requests are included.
V18.0-5 made available on 25 October 2019
This is a minor release
of change requests
V18.0-2 made available on 31 July 2019
This is a major release
of new facilitites, enhancements and change requests
In summary:
- A
new software option, Reinforced Concrete Frame Design, provides
design code checking of regular and arbitrary shaped reinforced
concrete beams/decks and columns/piers and piles subject to bending and
axial force.
- The
LUSAS Traffic Load Optimisation software option has been extended
to provide Rail Load Optimisation to a number of international
codes.
- The
Heat of Hydration software option has been extended to perform
hygro-thermal analysis, which models the time (hydration)
dependent behaviour of concrete from time of casting to old age.
- The
Steel Frame Design option now supports AASHTO LRFD 8th
edition.
- Steel
frame design checks to AS4100 now include axial load checks for
equal and unequal angles.
- Steel
frame design checks to EN1993-1-1 and EN 1993-2 now include
axial load checks for Class 3 angles.
- Steel
frame design checks to EN1993-2 now support Italy and Spain
National Annexes.
- Time
dependent prestress can now be carried out in accordance with
India code IRC:112-2011.
- The
restart facility is now supported by LUSAS Modeller.
- Nonlinear
concrete behaviours of cracking and crushing can be combined with
codified creep and shrinkage if required.
- Mohr-Coulomb
friction interface material now added.
- Design
code based load combinations can now be created in accordance with
the requirements of the EN1990 National Annexes of Finland, Italy,
Norway and Sweden.
- Combinations
and envelopes can now be examined to show the nested combinations
and envelopes that make up the definition, together with the
corresponding factors for each included loadcase, and the total
contribution.
- A
loadcase can now be created which includes all the loading
assignments and factors which gave a particular result (at a
particular node) for a smart combination.
- Creation
of influences and loadcases is faster when using the Vehicle Load
Optimisation option.
- Hygro-thermal and interface elements (for
soil-structure interaction) have been added.
- New
worked examples illustrate a number of the new facilities provided
in this release.
New facilities and improvements in more detail:
Reinforced Concrete Frame
Design (New software option)
Rail Load Optimisation
(included in the Traffic Load Optimisation software option)
Hygro-Thermal Analysis
(included in the Heat of Hydration software option)
Steel Frame Design
|
Post-tensioning enhancements
General modelling, material
and results improvements
Element library
General changes
New worked examples
|
Reinforced Concrete
Frame Design (New Software Option)
RC Frame Design
Design code checking of regular
and arbitrary shaped reinforced concrete decks/beams (and
piers/columns) with or without voids can now be easily carried
out in LUSAS Modeller. This is performed as a results
processing operation following the solving of a model, and
requires the inclusion of reinforcement arrangements within
the geometric line attribute as well as the assignment of
design code specific RC frame design attributes to lines
in the model that represent concrete members.
The following design codes are
currently supported:
- EN1992-1:2004
- EN 1992-1-1:2004 +A1 Eurocode 2: Design of concrete
structures Part 1-1: General rules and rules for
buildings.
- EN1992-2:2005
- EN1992-2: 2005 Eurocode 2: Design of concrete structures
Part 2: Concrete bridges - Design and detailing rules.
Design checks due to bending
with or without axial force can be carried out for reinforced
concrete sections at the Ultimate Limit State (ULS) and
Serviceability limit states (SLS).
RC Frame Design results
can be viewed:
- On the model
- Using the print
results wizard
- In tabular
format
- As
an interaction surface diagram
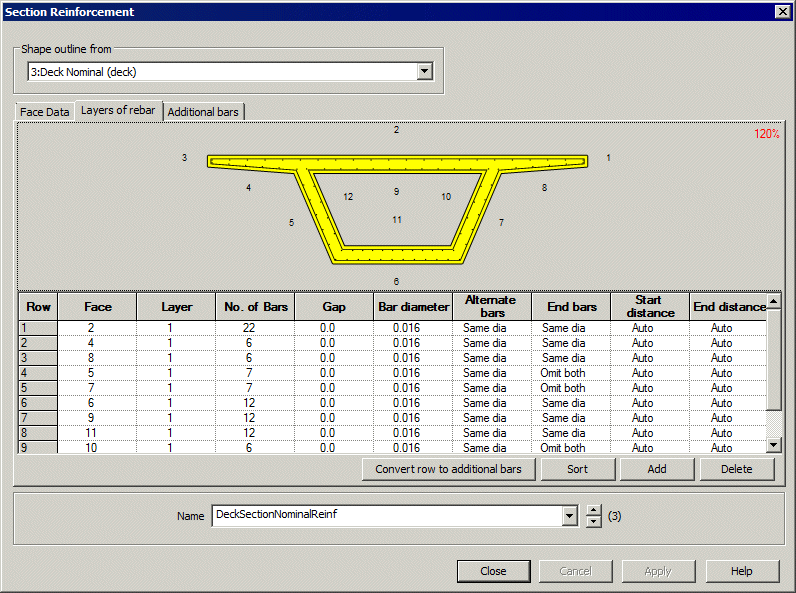
|
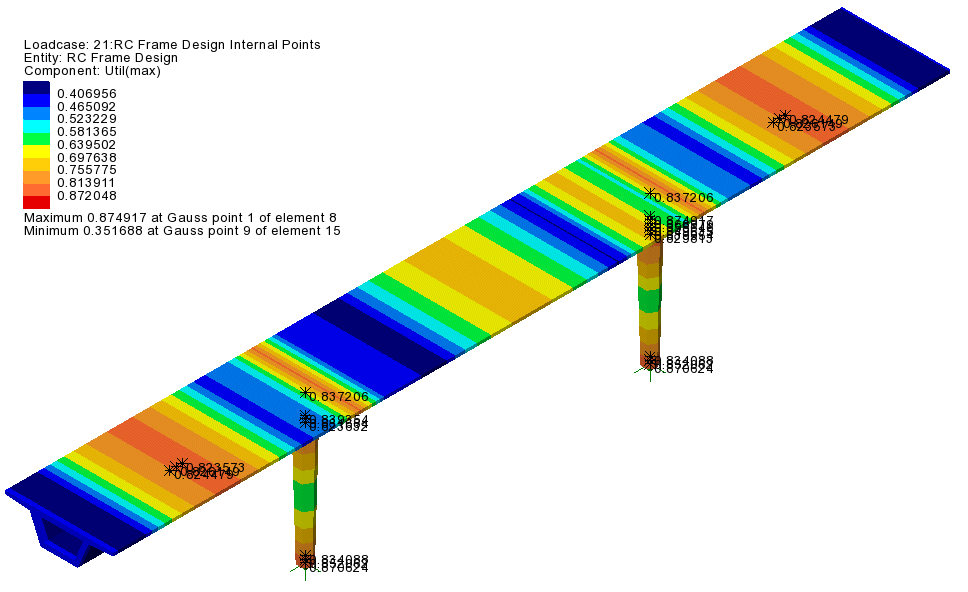
|
Section
reinforcement
|
Utilisation
plots
|
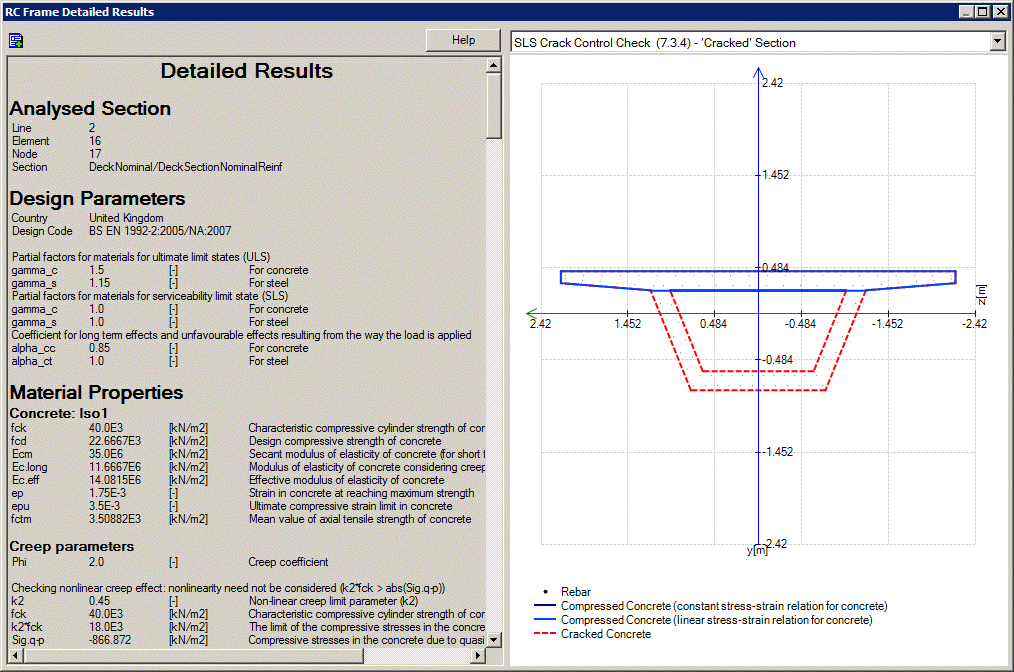
|
Detailed
results
|
|
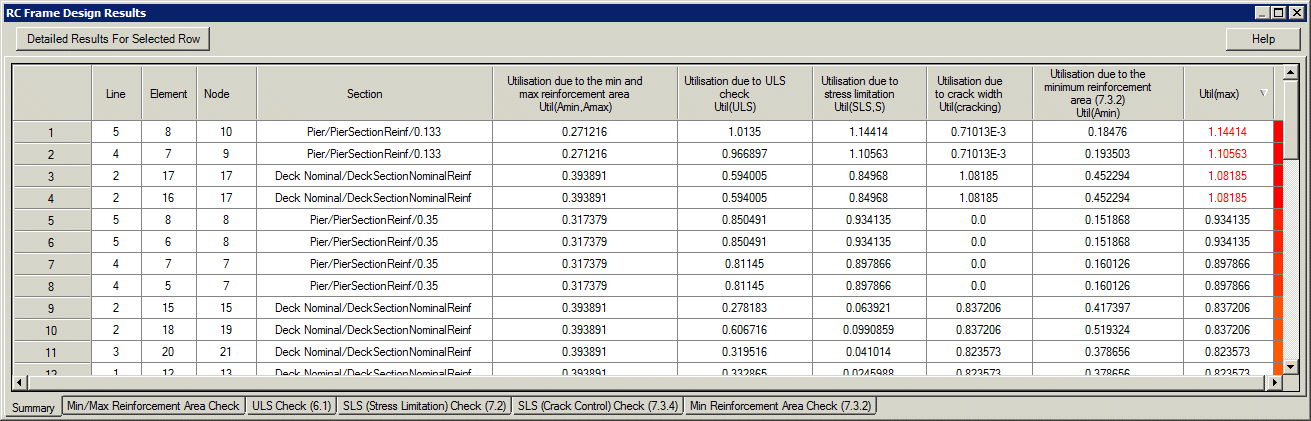
|
Summary
results
|
|
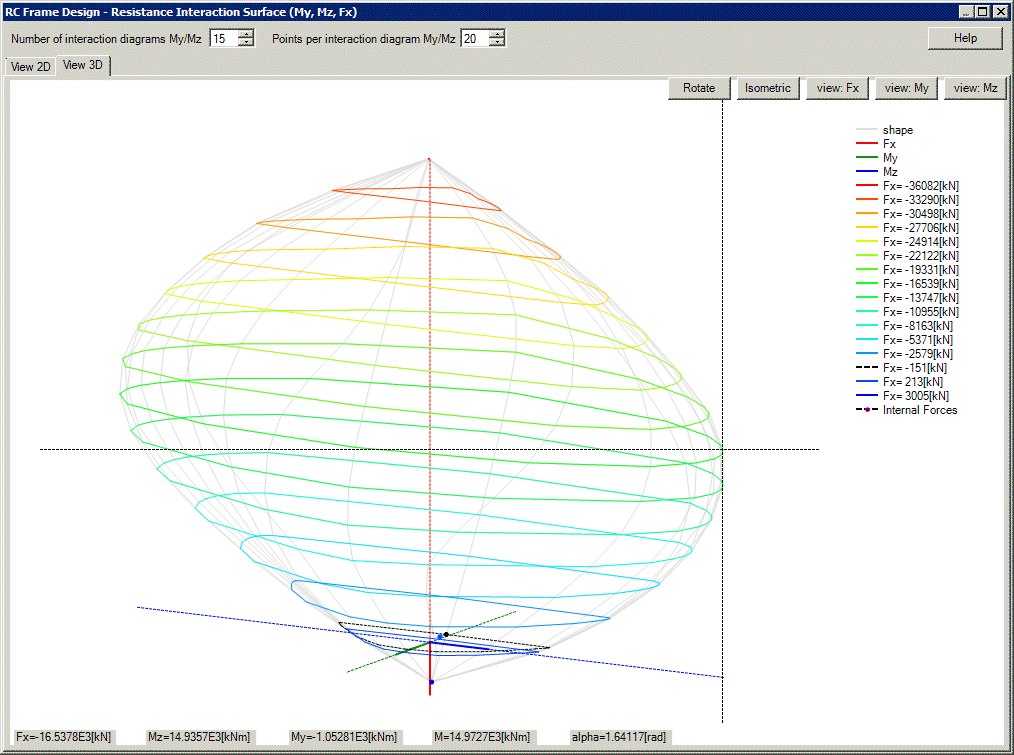
|
Interaction
diagrams
|
|
Defining
reinforcement
Section reinforcement
Section reinforcement defines
the bar arrangements to be provided in a member's
cross-section. Section reinforcement is a utility object
stored as an entry in the Utilities
Treeview and cannot be assigned to lines in the model
directly. Section reinforcement utilities are referenced by line
reinforcement utilities (that define the length over which
each section reinforcement utility acts along a line
representing a reinforced concrete member.)
The section reinforcement
dialog can be accessed from a reinforcement line dialog (by
selecting the 'New' option in the reinforcement section
droplist) or by using the Utilities > Reinforcement
> Section menu item. Section reinforcement can be
defined for any standard or arbitrary shape, with or without
voids. Tapering members are also supported.
Section reinforcement is
available for use with selected Bridge and Civil software
products only, and for licences that support RC
frame design. A model analysis
category of 3D must also be in use.
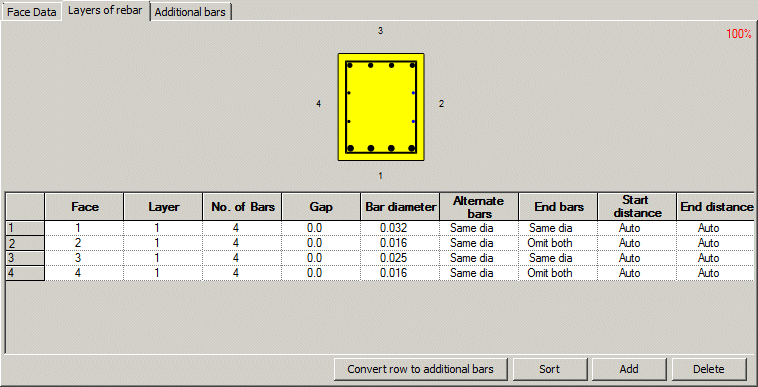
|
Defining
section reinforcement
|
Line reinforcement
Line reinforcement is
referenced by geometric
line beam attributes (that define the concrete section
size/shape and properties for a member). Line reinforcement is
used to specify how individual section
reinforcement arrangements apply over a length of a line
or lines representing a concrete member. Line reinforcement is
a utility object stored as an entry in the UUtilities
Treeview and cannot be assigned to lines in the model
directly.
The line reinforcement dialog
can be accessed from a geometric line attribute dialog (by
selecting the 'New' option in the reinforcement panel), or by
using the Utilities > Reinforcement > Line menu
item.
Line reinforcement is available
for use with selected Bridge and Civil software products only,
and for licences that support RC
frame design. A model analysis
category of 3D must also be in use.
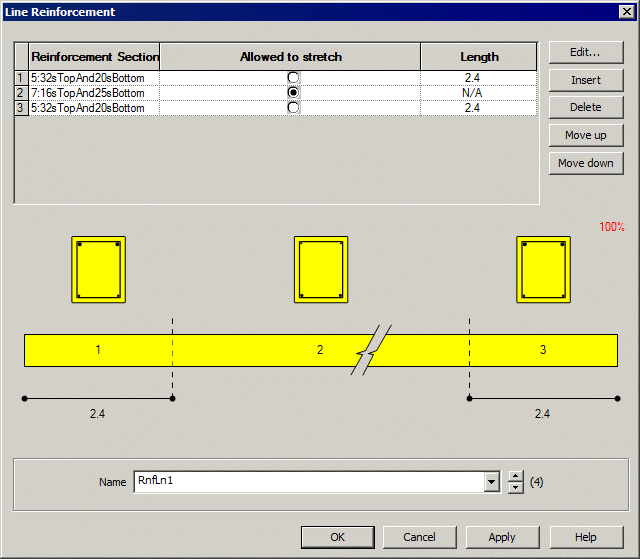
|
Defining
line reinforcement
|
Reinforced
concrete compound material model
A new
reinforced concrete compound material model has been
introduced for use with the RC
frame design facility. This material references linear
elastic concrete and steel materials provided in the standard
Material Library and permits the assignment of both materials
to a single line feature.
Reinforced
concrete material is defined by selecting the Attributes
> Material > Concrete (Reinforced) menu item. |
|
Rail Load
Optimisation (included in the Traffic Load Optimisation software
option)
Rail load optimisation
The LUSAS
Traffic Load Optimisation software option has been extended to
provide Rail Load Optimisation. This provides the means to
define parameters for a particular design code, and generate
the most critical rail track loading pattern for a selected
track layout, for each influence shape under consideration.
Rail Load
Optimisation currently supports track loading to:
- Eurocode
EN1991-2 (Recommended values) (p491ae) and National
Annexes for Denmark, Finland, Ireland, Italy, Norway,
Poland and the United Kingdom
- International
UIC Leaflet 776-1 (5th Edition)
- United Kingdom
NR-GN-CIV-025
To use the
Rail Optimisation facility requires the paths of railway
tracks to be defined and viable track layouts to be specified. |
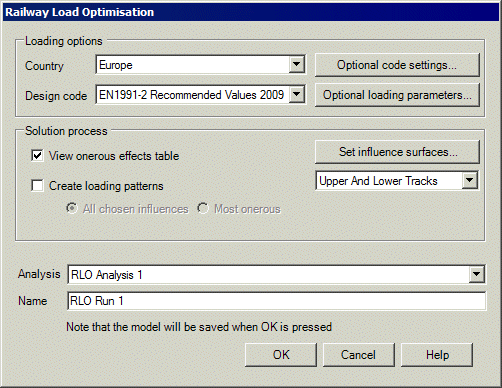
|
Track definition
Track definitions
are used by rail track layouts to specify particular track loading
scenarios for use with the Rail
Load Optimisation facility.
Track definitions
are defined by using the Bridge> Rail Track Optimisation > Track
Definition menu item. The centrelines of segments of track can be
defined by coordinates, or be copied and pasted from a spreadsheet, or
(more usually) be defined from selected lines and arcs that are drawn
to represent the track centrelines in the LUSAS model. The transverse
distance between rail loads on the track must also be stated.
Once defined, a
track is shown on the model by the drawing of additional lines to
represent the rails and sleepers. The rail track definition is stored
and viewed in the Utilities
Treeview. Like other utilities, track
definitions are not directly assignable to geometry and can only be
edited using this dialog.

|
Track
definition: Crossover Track (three straight lines
selected and a smoothing radius applied)
|
Track layouts
A track layout
defines which track
definitions can be loaded simultaneously in a Rail
DMI analysis. Track layouts are specified using the Bridge>
Rail Track Optimisation > Railway Track Layout menu item.
Multiple track layouts can be defined .

|
Track
Layout: Upper and Lower Track definitions included
|
Direct Method Influence
Analysis for Rail use
The DMI analysis capability has
been enhanced for use with the Rail Load Optimisation facility.
Instead of the grid of virtual points that is used by the Vehicle Load
Optimisation facility to represent the loadable region of a deck that
is to be loaded with a unit point load as part of an influence
analysis, for a Rail Direct Method Influence analysis, nodes are
created automatically where each rail intersects with an element in
the search area. In this way, the number of locations where a unit
load can be applied is minimised, and ensures that the influence
shapes are drawn following the alignment of each rail track.
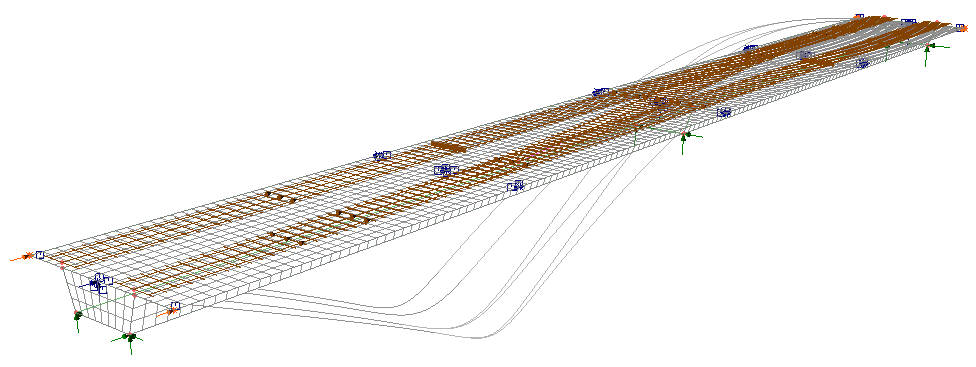
Hygro-Thermal
Analysis (included in the Heat of Hydration software option)
A hygro-thermal or coupled
hygro-thermal/structural analysis can be set-up via the New
Model dialog, or by adding a hygro-thermal analysis to a
structural analysis, or vice-versa. A Hygro-thermal /
Structural coupled analysis can model the time (hydration)
dependent behaviour of concrete from time of casting to old
age. It can:
- Take
into account the time dependent environmental conditions
when the concrete cures, such as daily cycles of
temperature and humidity, to the desired degree of detail.
- Model
the effect the formwork (and environment) has on the heat
and moisture transfer to and from the concrete
- Predict
the internal heat generated as the concrete cures so that
any excessive temperature gradients that might cause the
concrete to crack can be identified.
- Compute
the amount of shrinkage in the concrete as it cures via
the migration of moisture and the degree of saturation.
- Take
into account the creep strains that occur during cure as
the concrete is stressed.
- Model
the evolution of properties E, fc, and ft.
- Predict
failure when the concrete is fully (or partially) cured,
and if the mesh is fine enough, obtain reasonable
estimates of crack widths.
It can only be used when
concrete temperatures are under 100 degrees Celsius, as it
assumes that the pore pressure remains constant (i.e. the rate
of pore water evaporation is low in comparison to the rate of
water vapour migration in the porous network).
|
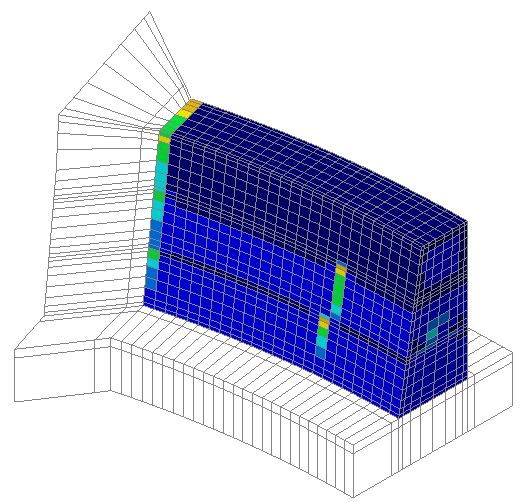
|
Hygro-thermal
modelling templates provided
2D, 2D axisymmetric and 3D startup
templates are provided for use with the hygro-thermal facility. These
can be chosen on the New Model dialog following the selection of an
appropriate analysis category.
Hygro-thermal
material models
Hygro-thermal
isotropic materials can now be defined by using the Attributes>
Material> menu item, providing a hygro-thermal
analysis entry is present in the Analyses
Treeview. Isotropic
hygro-thermal material is applicable to all thermal elements
except thermal links (see the Element
Reference Manual)
For a hygro-
thermal analysis two material types are available:
- Hygro-thermal
concrete (for concrete)
- Hygro thermal
(for general use, and for use with concrete)
Hygro-thermal material
properties are applicable to hygro-thermal elements only. If a
hygro-thermal element is to represent a non-porous material
(e.g. steel) it should be assigned thermal isotropic
properties.
|
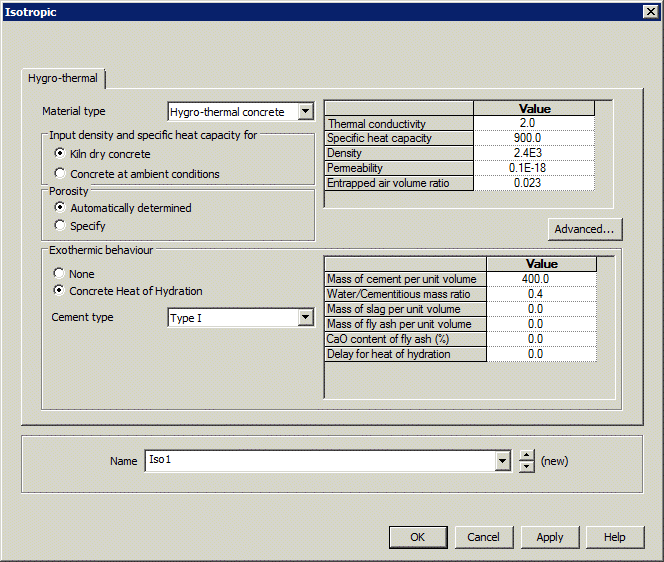
|
Hygro-thermal
loading
A range of
hygro-thernal load types is provided when carrying out a hygro-thermal
analysis.
Hygro-thermal
supports
Prescribed
temperature and prescribed relative humidity can be defined when
carrying out a hygro-thermal analysis.
Assign
environmental temperature within a load curve analysis
If external fluid
(air) temperature and/or associated convection and/or radiation heat
transfer coefficients and/or environmental relative humidity and/or
water vapour mass transfer coefficients vary in time, pre-defined or
new 'on-the-fly' load curves can be specified on the Environmental
conditions assignment dialog in order to vary each of the values
accordingly.
Steel Frame Design improvements
Steel frame
design to AASHTO LRFD 8th edition
The steel frame
design software option now supports AASHTO LRFD 8th edition. The
scope of the checks to the 8th Edition is also greater than that of
the previously implemented 7th Edition, covering:
- Shear
checks for members with transversely stiffened webs – with
provision for different end panels and interior panels
- Design
checks for S-series (rolled standard beams)
- Design
checks for equal-thickness angle sections with a leg ratio <1.7
(for axial loads only)
- Option
for user-defined buckling lengths
- The
method for checking nonslender members subject to combined
compression and flexure of Article 6.9.4.2.1 has been implemented
- Inclusion
of ASTM A1085 product standard for hollow sections (new in the 8th
Edition)
Steel frame
design to AS4100
Steel frame design checks to AS4100 now
include axial load checks for equal and unequal angles.
Checks for angle sections are limited
to Util(Fxt) - utilisation
for tension, Util(Fxc) -
utilisation for compression, Util(Fx)c,by)
- utilisation for compression member about the y-axis, and Util(Fx)c,bz)
- utilisation for compression member buckling about the z-axis.
Steel frame
design to EN1993-1-1 and EN1993-2 enhanced
Steel frame design checks to EN1993-1-1
and EN 1993-2 now include axial load checks for Class 3 angles.
In addition to choosing line or
combined line the option of a user defined length has been included
for buckling lengths. In addition the length for lateral torsional
buckling is now explicitly defined. The lateral torsional buckling
details for models created in versions 16.0 and 17.0 will be based on
the minor axis buckling details.
Steel frame
design to EN1993-2 now supports Italy and Spain National Annexes
- Italy
(UNI-EN 1993-2/NA:2007)
- Spain
(AN/UNE-EN 1993-2:2013)
Updated
steel section properties for AISC9 steel sections
Section library shapes and properties
for the following AISC9 steel sections have been updated to
include properties for sloping flanges:
- S Shapes
- C
Standard Channels
- MC
Micellaneous Channels
- TS tees
from S Shapes
Post tensioning
enhancements
India IRC:112-2011
Time dependent
prestress can now be carried out in accordance with India code
IRC:112-2011. Appropriate material properties have also been added to
the Material Library.
General modelling, material and results
enhancements
Restart facility
now supported by LUSAS Modeller
When a nonlinear
or time-step analysis has failed for some reason and a re-solve is
required from that point, or if a solution is to be deliberately
continued from a specified stage reached in a previous solution, a
Modeller restart setting can now be used. The Modeller restart
facility enables failed or terminated analyses to be restarted from
the last saved increment or, alternatively, if a solution is to be
deliberately continued from a specified stage reached in a previous
solution, from a specified loadcase.
Codified
concrete creep material with nonlinear cracking
Concrete material is now no longer
defined by visiting the isotropic and orthotropic material dialogs as
required in previous versions. This is now done by selecting the Attributes>
Material > Concrete (Nonlinear) menu item. Concrete can
now be defined with or without respect to a design code, and can
include creep and/or shrinkage if a design code supports it.
A new transient smoothed concrete
material model (model 105) has been introduced. The model is
fundamentally the same as concrete smoothed concrete material model
(model 109), but can only be accessed if a hygro-thermal/structural
coupled analysis is specified. The material model takes into account
the effects of heat of hydration, creep and shrinkage, along with the
hydration dependent evolution of properties E, fc
and ft.
When a pre-version 17 model is loaded
that uses older versions of concrete models such as Cracking concrete
model 82, Cracking with crushing (model 84), Multi-crack (model 94) -
those models will be listed in the concrete material droplist in
addition to the current valid concrete models.
Mohr-Coulomb friction
interface material
The Mohr-Coulomb friction interface
element complements existing facilities for soil analysis and allows
for more accurate modelling of strain hardening, softening and
dilatancy at a soil/structure and soil/soil interfaces.
The Mohr-Coulomb interface material can
be used in conjunction with 2D and 3D interface elements. It permits
the modelling of a standard elastic-plastic sliding interface as well
as strain hardening, softening and dilation. The classic Mohr-Coulomb
relationship is used to define failure conditions on the interface,
and the slip at the interface is used to control the rate of dilation
as well deterioration in the angle of friction. Cohesion can also be
linked to the slip.
Additional
design load combinations
Design code based load combinations can
now be created in accordance with the requirements of the EN1990
National Annexes of Finland, Italy, Norway and Sweden.
Separate Design Combination parent
folders are created for Basic and Smart Combinations in the Analyses
Treeview, containing folders holding the SLS Characteristic, SLS
Frequent, SLS Quasi-permanent, and ULS Persistent (Eq 6.10) load
combinations.
Examine the
definition of a combination or envelope
By selecting the Examine definition
context menu item for a combination or envelope entry in the Analyses
Treeview, it is now possible to view, in a treeview form, the
nested combinations and envelopes that make up the definition,
together with the corresponding factors for each included loadcase.
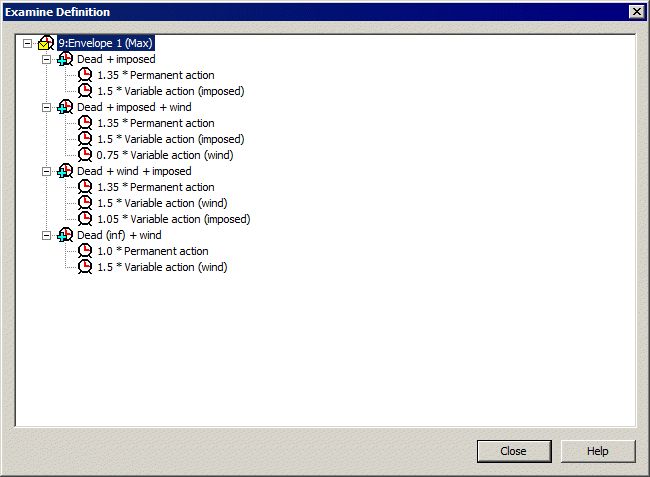
Examine computed
results for combinations and envelopes
Two new selections are available in the
Print
Results Wizard 's results output table to allow users to examine
and show how a selected combination or envelope or other loadcase
result has been obtained. The options make it easier to identify the
logic behind, dominant contributors to, and factors included within
the load effects which may be used for subsequent design checks for a
selected results value:
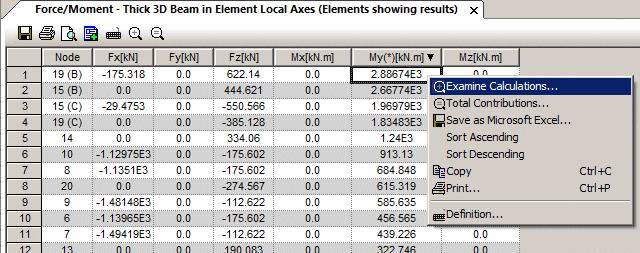
Examine calculations
- Examine
calculations
Shows how a selected value has been calculated by listing the
envelopes, combinations or loadcases, and the values from each,
along with the relevant factors applied, that produce the selected
result.
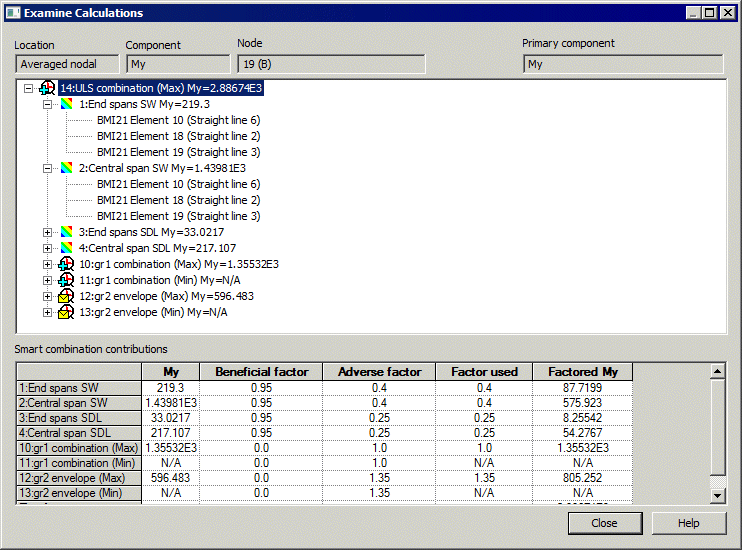
Total contributions
- Total
contributions
For a selected results value, selecting this option reduces the
contributing envelopes and combinations to a single table of
loadcases and factors in use. Where it is notionally valid to sum
the contributing unfactored load effects, these values are also
listed in the table generated.
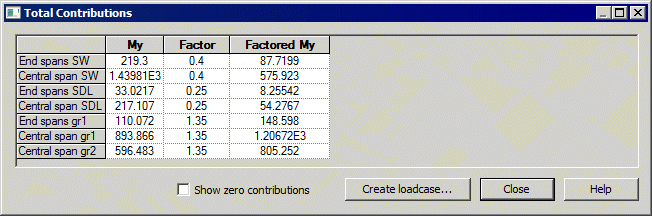
Create
a loadcase from a smart combination result
When viewing print results wizard
output for a smart combination, a loadcase can be created which
includes all the loading assignments and factors which gave a
particular result (at a particular node). This is done by clicking the
‘Create loadcase button on the Total Contributions dialog.
This may be useful for various reasons including when engineers wish
to use an onerous loadcase identified by a linear analysis as part of
a further nonlinear analysis.
Element library
Hygro-thermal
elements
- New
2D plane hygro-thermal elements (THT3,6 and QHT4,8) - used for
analysing continuum problems involving the heat of hydration
and/or drying (wetting) of concrete when behaviour is essentially
two dimensional. These elements are normally used in a
hygro-thermal-structural coupled analysis. They can be coupled
with plane strain structural elements (since the heat/moisture
exchange over the area of the element would have effect only near
both ends of the ‘infinite’ thickness), or with thin, plane
stress elements, when they are ideally isolated on both sides of
their area.
- New
2D axisymmetric hygro-thermal solid elements (TXHT3,6 and
QXHT4,8) - used for analysing continuum problems involving the
heat of hydration and/or drying (wetting) of concrete, which
exhibit geometric and loading symmetry about a given axis. These
elements are normally used in a hygro-thermal-structural coupled
analysis.
- New
3D solid hygro-thermal elements (THT4,10, PHT6,12,15 and
HHT8,16,20) - used to analyse continuum problems where the
response is fully 3D (i.e. it cannot be approximated using the
plane or axisymmetric elements). These elements are generally used
for problems involving the heat of hydration and/or drying
(wetting) of concrete, and are normally used in a
hygro-thermal-structural coupled analysis.
Interface
element for soil-structure interaction modelling
- New 2D (IPN6P and
IAX6P) and 3D (IS12P and IS16P) two phase interface elements -
used for modelling standard Mohr-Coulomb friction contact in
soil/structure and soil/soil interactions.
User change requests
In addition to the range of new
facilities and improvements listed, many user change requests have
also been implemented. The originators of all requested changes to the
software (some of which are included in the above list of
enhancements) that have been incorporated in this release will be
notified individually.
Documentation
User manuals
All online and printed documentation
has been updated for this new release. Manuals are provided in PDF
format as part of any LUSAS installation, and are also available for
download from the LUSAS website.
New Worked
Examples
The following new
examples illustrate some of the new facilities provided in this
release.
- RC Frame
Design to EN 1992-2
- Railway
Load Optimisation
- Early-age
Hygro-Thermal Cracking of a Concrete Dam
- Balanced
Cantilever Construction of a Segmental Post Tensioned Bridge
- Add
a user vehicle to the vehicle load optimisation facility
Other
worked examples
All existing worked
examples have been updated to match changes made to the software.
Individual worked
examples in PDF format are provided as part of the LUSAS software
download file or release DVD, and are also available from the online
help. Examples are also available from the LUSAS User Area.
Other
Potential issues
opening PDF files referenced in CHM files
On some PCs, and for certain operating
systems, the installation of security updates as released by Microsoft
can affect the opening of PDF files from the table of contents panel
within the CHM file-based help. Any links to PDF files from within
help topic pages may similarly be affected.
If problems are found
when attempting to open these files from within the online CHM file
supplied please note the following:
- Selected
manuals are supplied in PDF format on the installation kit and
these are normally installed into the <LUSAS Installation
Folder>/Programs/PDF_Manuals folder.
- Workarounds/solutions
may be provided by Microsoft during the availability and support
of this particular LUSAS software release.
Previous new facilities and improvements in
this release
None, this is the first release of
Version 18.
|