Case Study
Enabling Rammer to Hit Harder
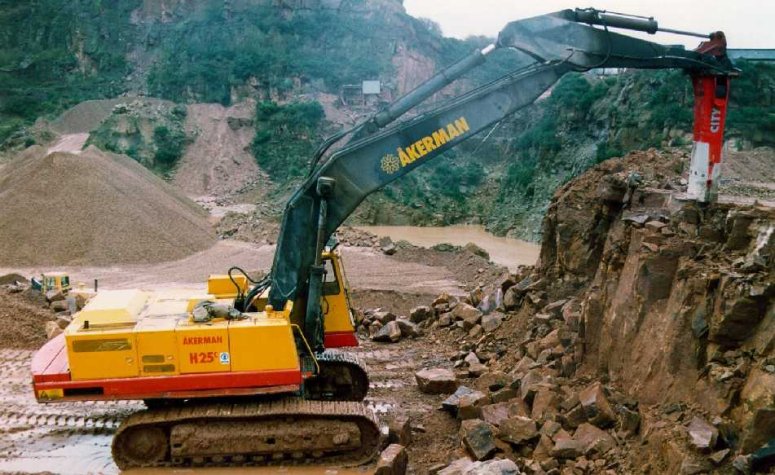
Rammer, part of
Sandvik Mining and Construction in Finland, manufactures hydraulic attachments for rock
excavation, demolition and recycling. The company have been users of LUSAS for many years,
analysing hammer parts, hammer housings and cutter-crusher and pulverizer parts for their
Rammer range of products. Rammer is recognised as a world leader in the design and
manufacture of hydraulic hammers for primary and secondary breaking work.
The 1m long cylindrical piston of a large hammer is made from
case hardened steel and weighs over 200 kg. The piston strikes a work tool with a velocity
approaching 10 m/s. Transient 3D dynamic analysis using LUSAS Analyst was necessary to
understand what happens to the piston and tool as a result of the impact. Of particular
interest during the initial analyses was the degree of bending caused by the tool being
driven at an inclined angle to the ground. As a result of using LUSAS a better
understanding of the effects of an inclined impact was obtained.
Due to symmetry only half of the piston
needed to be modelled in LUSAS. Approximately 840, three-dimensional solid elements having
linear material properties modelled the piston and joint elements with nonlinear material
properties representing the ground that the tool strikes. Slidelines automatically
modelled the contact between the piston and the tool. The initial load case was the
velocity of the piston towards the tool. Typically, 120 time steps modelled the impact
event using a time step of 10 microseconds.
From the results obtained, the displacements caused by the bending load
cases were of particular interest. The analyses showed that when the tool is
asymmetrically thrust against the ground, the tool bends highly with the bending stress
wave propagating into the piston causing it to bend as well. The degree of bending
experienced by the piston was unexpected indicating that it may be necessary to try to
reduce inclined impacts when operating with a hydraulic hammer. It also indicates the
importance of supporting the piston with good bearings to avoid seizure effects.
Eero Ojala, the engineer responsible for the analysis
found LUSAS straightforward to use. He said: "Contact between the piston and the tool
was easy to model in LUSAS with the slideline technique being especially useful. As an
extension to this work, it would be interesting to model the whole hammer body to see what
happens when the piston and tool are perfectly supported in relation to it".
"Contact between the piston and the tool
was easy to model in LUSAS with the slideline technique being especially useful."
Eero Ojala, Rammer
Other LUSAS Analyst case
studies:
|