Software Tour
Analysis software for composites engineering
LUSAS
Composite contains a comprehensive range of unrivalled
engineering analysis facilities to cater for all types of composite
design.
From simple failure prediction using a number of failure
criteria including Tsai-Hill, Hoffman and Tsai-Wu through to
advanced delamination failure modelling, LUSAS Composite will help
shorten your design and checking times giving reliable results every
time.
For structural and
bridge applications, model Fibre Reinforced Polymer (FRP),
laminated glass, reinforced concrete using
the smeared reinforcement technique, and carry-out gradual
through-thickness masonry arch cracking assessments using layered
shell elements.
The intuitive Windows
user interface gives easy access to the full range of powerful
modelling and results processing facilities, together with on-line
help. Regarded as a leader in engineering
analysis, LUSAS Composite is rich in powerful and advanced
features to meet your analysis needs and extend your design
capabilities.
Many real-life
illustrative uses of the software can be seen by visiting our
engineering case studies
page.
Why use LUSAS
Composite?
- Provides cost-effective structural modelling and analysis
of all types of composite component, in one
software package.
- Feature-based
modelling that allows mixing of element types in
the same model.
- Benefit from
advanced nonlinear
geometry, material and contact modelling
- Customise the
softtare using the LUSAS Programmable Interface.
- LUSAS is a
long-established and trusted provider to industry leaders, and
LUSAS Technical Support is stated, by its users, to be simply:
"The best in the business."
Ideal
for all types of composite analysis
By using the unrivalled
state-of-the-art element libraries and material models of LUSAS Composite
a host of composite engineering problems can be solved.
- Built-in associativity ensures
that if the model geometry is amended, all assigned loadings,
supports and other attributes are automatically moved to suit.
- Extensive GUI results processing
facilities allow extensive contouring, graphing and plotting of
composite specific results.
- By using the advanced scripting
language facilities, user-defined menus and forms can be added
allowing specific repetitive analysis tasks to be performed with
a minimum of user involvement.
- Complete analyses from modelling
to results processing can be automated - and all tailored to
your way of working.
Advanced analysis and
design
Advances in composite technology
require advanced software solutions. LUSAS Composite offers
these solutions now to give you the edge over your competitors.
LUSAS Composite gives you:
- An advanced element set.
- Use of all LUSAS material models.
- Fast Iterative Solver Technology.
- Access to advanced analysis
options.
A software key system means that you
can call us at any time for a key to unlock these powerful options
so that you can tackle new analyses straightaway.
Easy
lay-up definition
LUSAS Composite offers a
quicker and simpler way than ever before to define composite lay-ups
independent of the component to be analysed. The properties of each
laminate are defined in a table and each layer given a unique name
for use in results processing - extremely useful where ply drop off
occurs. A lay-up icon provides a useful visual check before the
lay-up is automatically assigned to the underlying geometry. These
unique lay-up procedures dramatically reduce the chance of errors.
Advanced analysis
technology
Because composite components have
different failure characteristics to non-composite components and
are often a complex combination of materials, they pose unique
analysis problems. The use of traditional modelling techniques for
composites can be prohibitively expensive due to the large number of
elements required. Whilst some analysis systems allow laminate
properties to be integrated together to form an homogeneous material
matrix, such systems can only predict failure with a linear
analysis. To model failure correctly, and to assess the residual
strength, nonlinear analysis with LUSAS Composite is
necessary in which the individual laminate behaviour is modelled.
Advanced
composite elements
In addition to shell elements, the
LUSAS 3D solid composite element reduces the model size by allowing
a number of laminates to be modelled by a single element. Where
complex 3D components are built from a number of composite blocks
butted together LUSAS Composite can be used to
automatically generate constraint equations to tie dissimilar meshes
together. This powerful facility can also be used to provide rapid
mesh grading of elements in high stress areas giving you faster
solution times. In addition, linear and nonlinear modelling of
adjacent laminates is possible, allowing you to analyse mixed
material lay-ups.
Composite failure
criteria
Composite failure criteria provide a
means of predicting composite failure from the linear stress
distribution. Within LUSAS the commonly used Tsai-Hill, Hoffman,
Tsai-Wu (with Cowin extension), and Hashin (fibre and matrix)
composite failure criteria are available.
Composite matrix
failure modelling
The Hashin composite damage model has
been implemented to model matrix/fibre failure in composite
materials. The model can be used with the LUSAS solid composite
elements. A set of failure criteria have been used to represent
fibre and matrix failure. These failure criteria result in a
degradation of the Young’s modulus, shear modulus and Poisson’s
ratio where the damage has occurred. Unlike the composite failure
criteria, matrix failure modelling can model progressive failure
using a nonlinear analysis.
Composite
delamination
Both 2D and 3D composite delamination
interface elements are used in LUSAS Composite. These
elements enable composite delaminations to be modelled using an
incremental nonlinear analysis. Interface elements are embedded into
the finite element model and assigned delamination properties using
a nonlinear material model. If the strength exceeds the strength
threshold value in the opening or tearing directions the material
properties of the interface element are reduced linearly as defined
by the material parameters and complete failure is assumed to have
occurred when the fracture energy is exceeded. No initial crack is
inserted so the interface elements can be placed in the model at
potential delamination sites where they will lie dormant until
failure occurs.
Comprehensive
nonlinear analysis
LUSAS Composite has superior
nonlinear problem solving capabilities.
- Powerful facilities for geometric,
material and boundary nonlinearity are available for problems
involving large deformations, plasticity and collapse.
- Fully automatic load
incrementation, automatic recovery from convergence failure and
restart features are all designed to enable newcomers to
nonlinear analysis to quickly become proficient in solving a
wide variety of nonlinear problems.
- Results processing facilities
provide automatic load-displacement graphs and viewing of
yielded material.
Impact and contact
analysis
For low or high speed impact and
contact problems, contacting elements are automatically detected and
specially developed ‘slidelines’ and ‘slidesurfaces’ handle
the interaction that takes place at contacting regions greatly
simplifying your analyses in 2D or 3D.
Dynamic analysis
Forced response, vibration and
transient dynamics problems can be solved quicker with LUSAS Composite
and, if you wish, by calculating the response for selected loadcases
using the Interactive
Modal Dynamics (IMD) results processing facilities. This gives
shorter analysis times and reduced disk usage compared to a full
transient dynamics assessment.
Working with CAD data
Model information can be exchanged
with a wide range of CAD systems using industry standard exchange
formats such as IGES and DXF, as well as directly with specific CAD
systems using proprietary data exchange formats.
Structural
applications
For structural
and bridge applications, modelling of Fibre Reinforced Polymer (FRP),
laminated glass, reinforced concrete using
the smeared reinforcement technique, and gradual
through-thickness masonry arch cracking assessments can be carried out using
the advanced layered shell elements.
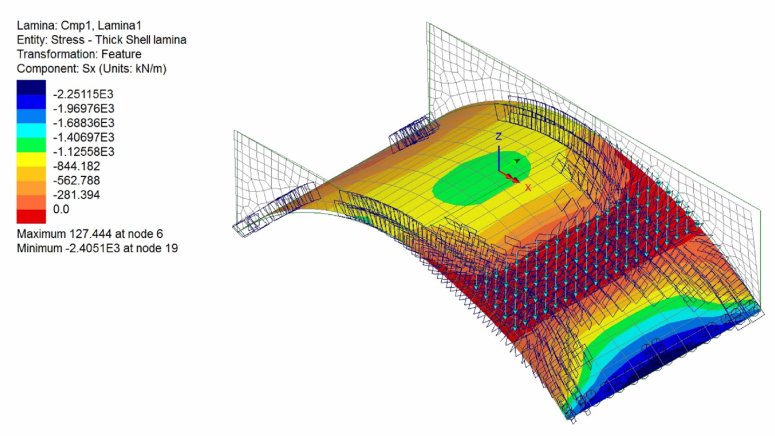
Software
products
LUSAS
Composite is
available as only one software product version, Composite Plus. The Windows user
interface provides for easy and rapid model generation, load
application and combining of loadcase results.
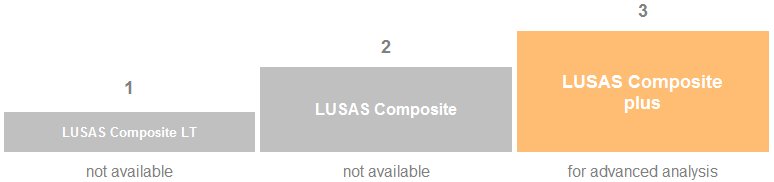
Usage
Element
sets
Software
options
The finite
element analysis capabilities of LUSAS Composite can be extended by
purchasing additional software options.
LUSAS
High Precision Moulding
To accurately
predict the distortion of laminated composite parts during manufacture
and provide reverse engineered surfaces to create "right first
time" tooling LUSAS offers a consultancy service
using its specialist LUSAS High Precision Moulding (HPM) software
product. By using
this service considerable savings can be made in time to market,
manufacturing time and costs are less, assembly stresses are
lowered, and the time-consuming fitting of any shims is
eliminated. |
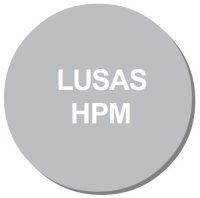
|
Global
coverage and support
LUSAS software is
marketed and supported globally by LUSAS and also through a network of
distributors and resellers that cover every continent.
Used by thousands of
users, LUSAS is highly regarded in industry, as demonstrated by an impressive list of
clients, which include many of the top international consultancies.
LUSAS software is also used extensively by government agencies, local
authorities and smaller to medium-size consultants, many of whom find
that the advanced analysis facilities not only expand their
capabilities but also give them a competitive edge.
Universities and
research institutions throughout the world use the academic version of
LUSAS, which provides a steady supply of proficient LUSAS users to
support your use of the software in your industry.
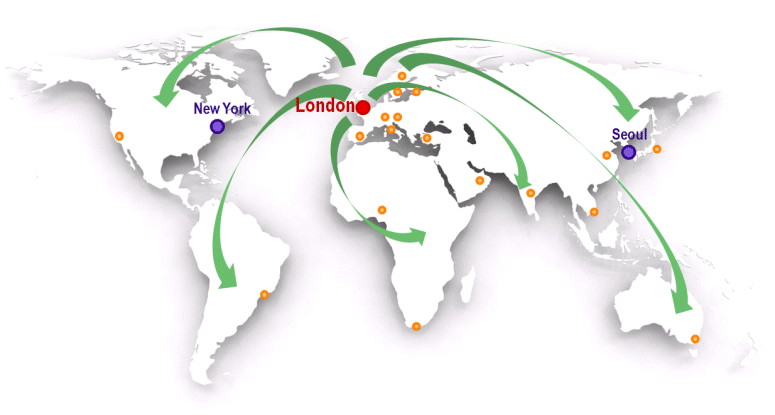
Find out more
|