|
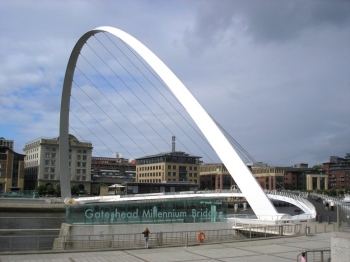
|
Support Hinge Assemblies for the
Gateshead Millennium Bridge
|
"With
LUSAS, we optimised the distribution of material to give the
minimum weight and cost for the applied loading and got more
accurate answers than we would have done by other
means."
Phil
Snowsill, Senior Design Engineer, Kvaerner Markham |
|
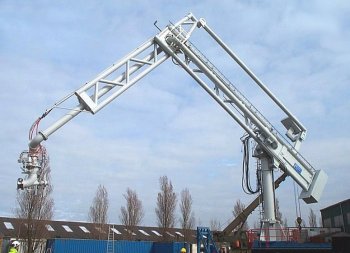
|
Stress
and thermal analysis of a marine LNG loading arm
|
"By
employing LUSAS as an independent consultant Woodfield
Systems were not only able to confirm or adjust their
designs to ensure that they met the best possible design
conditions but were also able to provide complete confidence
to their client that the designs used would provide trouble
free operation, improve vessel turn-around and give
longevity of service." |
|
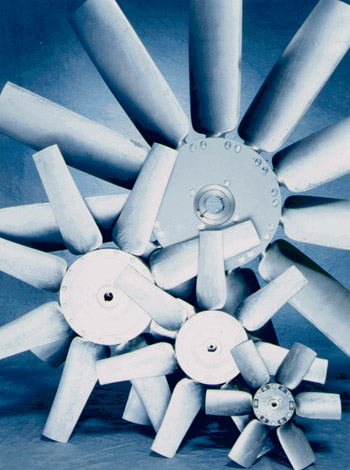
|
Design optimisation of an axial impeller hub
|
|
|
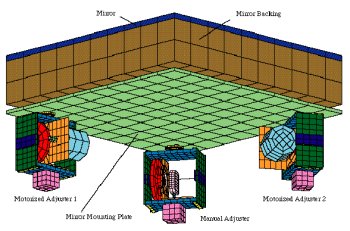
|
The design
and analysis of a laser mirror assembly
|
|
|
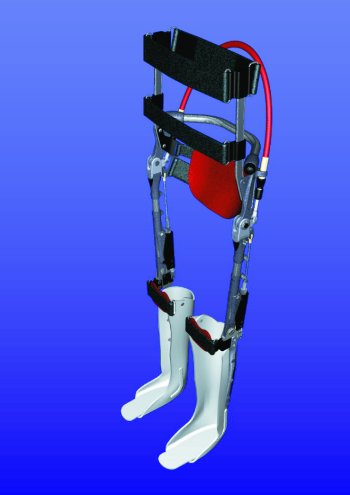
|
Optimising reciprocating gait
orthoses
|
|
|
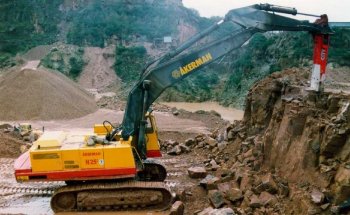
|
Enabling Rammer to hit harder
|
|
|
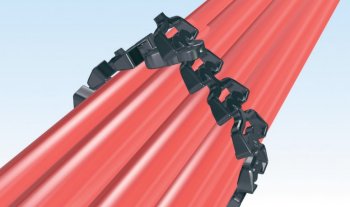
|
Innovative cable tie
design
|
"The results produced from LUSAS
Analyst made it
possible for us to optimise the shape and dimensions of the cable tie cells to give the
performance we required for the specified loading conditions."
Andy Harsley, Technical
Director, Millepede Cable Ties
|
|
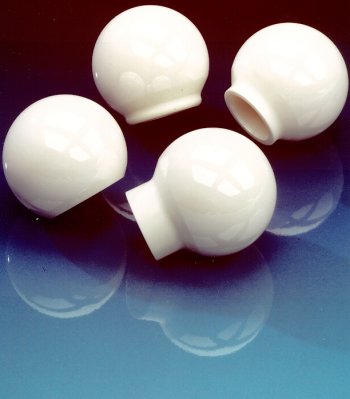
|
Contact analysis of artificial hip joint
components
|
|
|
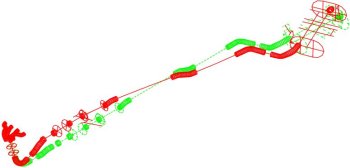
|
Faster vibration analysis of vehicle exhaust systems
|
"Our evaluation of proposed new exhaust systems can
now be performed at least twice as fast as previous methods with greater accuracy also
being achieved."
Ian Rutherford, CAE Team Leader,
Arvin Exhaust R&D
|
|
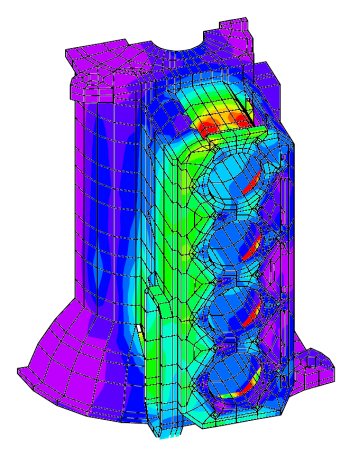
|
Engine analysis with
LUSAS and lasers
|
|
|
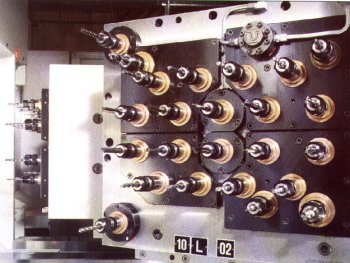
|
Automated dynamic
analysis of high speed drill spindles
|
|
|
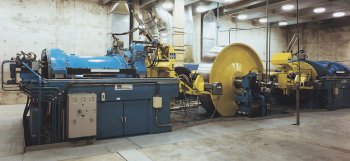
|
Innovative dynamometer
design
|
"We specialise in undertaking novel
engineering challenges so we need analysis software that provides reliable answers for any
type of analysis problem. LUSAS Analyst meets our needs in this respect and helps
to enhance our in-house design skills in a very cost-effective way".
Bill Coleman, Director at Design & Projects
|
|
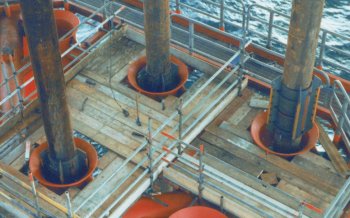
|
Offshore
centraliser design
|
|
|
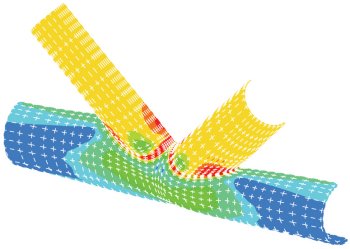
|
Fatigue analysis of tubular joints
with single-sided welds
|
|
|
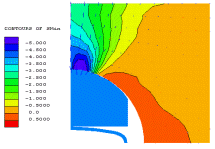
|
Pressure sensor for
monitoring mine safety
|
"The solutions to
these problems were far from obvious so we turned to FEA (Australia) Pty Ltd for advice.
The support we got was marvellous, with FEA coming up with some truly innovative solutions
and not resting until we had achieved our objective".
Ken McNabb, Mincad Systems
|
|