Case Studies and Links to Academic
Papers
LUSAS Academic
is used by universities, research institutes and teaching colleges
worldwide for all types of finite element analysis.
These case studies provide a
number of illustrative uses of the software with the most recently added
article at the top.
|
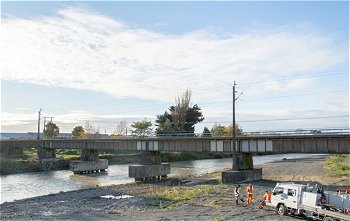
|

Field
measurement and simulation of the dynamic response of a
railway viaduct
-
Mehrdad
Bisadi, a PhD researcher at the University of Auckland,
is using LUSAS to investigate the accuracy and
reliability of the impact factors used to design and
assess New Zealand rail bridges. The objective has been
to fine-tune a LUSAS Bridge model prior to carrying out
numerical modelling of the dynamic response of the
viaduct for different train dynamic characteristics. A
weigh-in-motion system measured the train
characteristics during field monitoring. The measured
data was then used to define the train configurations in
the LUSAS software. Interactive Modal Dynamics analysis
with LUSAS computed the dynamic response of the viaduct
during train crossings. A comparison between the
measured and simulated results showed that the LUSAS
model accurately predicts observed displacements.
|
|
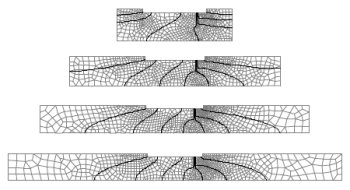
|

A
Strategy for Teaching Finite Element Analysis to Undergraduate Students (414k)
- The analytical power and design flexibility offered by
the Finite Element Method (FEM) can be all too readily masked from the first time user by
its apparent complexity. The steep learning curve can appear daunting when the method is
first encountered, and FEM needs to be sensitively introduced, with carefully graded
examples if students are not to be put off the subject completely. In this paper the
author describes a strategy which he believes enables students to experience for
themselves how beneficial FEM can be, whilst at the same time, warns them of the pitfalls
and potential dangers.
|
|
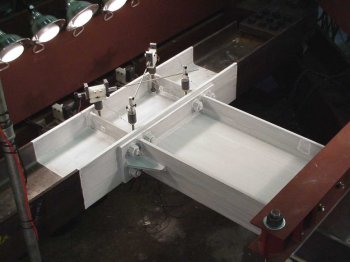
|

Finite
Element Analysis of Structural Steelwork Beam to Column Bolted Connections (423k)
-
A combination of simple fabrication techniques and speedy
site erection have made bolted endplates one of the most popular methods of connecting
members in structural steelwork frames. Although simple in their use, bolted endplates are
extremely complex in their analysis and behaviour. This paper reports on a Steel
Construction Institute funded PhD research program which uses a combination of full scale
testing and materially non-linear three dimensional finite element analyses (FEA) in order
to investigate extended end plate beam-to-column connections.
See also the LUSAS Civil
& Structural case study Beam
/ Column Moment Connection Research
|
|
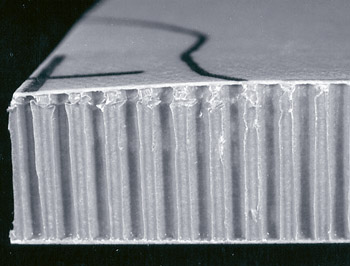
|

Finite
Element Analysis of Impact Damaged Honeycomb Sandwich Panels (515k)
-
Due to high stiffness and strength to weight ratios,
composite sandwich is used increasingly in aerospace applications. The main drawback of
sandwich structure is its low resistance to impact damage and the extent to which the
strength of the structure is reduced under compressive loading. In this study, it is
proposed that a continuum damage model is used to model crushing due to impact. The model
describes the compressive behaviour of honeycombs made from materials that are prone to
elastic buckling. The material behaviour in compression is described by a combination of
three constitutive models namely elastic, continuum damage and inelastic strain
accumulation. The model has been interfaced with LUSAS and is used to model
soft impacts onto minimum gauge Nomex sandwich. The materials and
dimensions are typical of sandwich panels found in commercial aircraft. Results from the
LUSAS analysis are compared to experimental data and are found to compare
well.
|
|
Performing online
searches for academic and
commercial papers citing LUSAS
-
By
entering lusas paper filetype:pdf into Google (or other
search engines) many published papers citing LUSAS can be seen.
-
By
adding more keywords such as steel or concrete or bridge
or soil you can isolate particular applications.
-
A
keyword search of +lusas +paper +steel +bridge filetype:pdf would
only list papers with a steel bridge ‘flavour'
-
Using
the + symbol in front of a keyword only gives results with
those keywords present and helps return results containing lusas and
not words such as lucas for instance.
Commercial Case
studies
Find out more
|
|
Software Information
|