Case Study
Offshore Centraliser Design
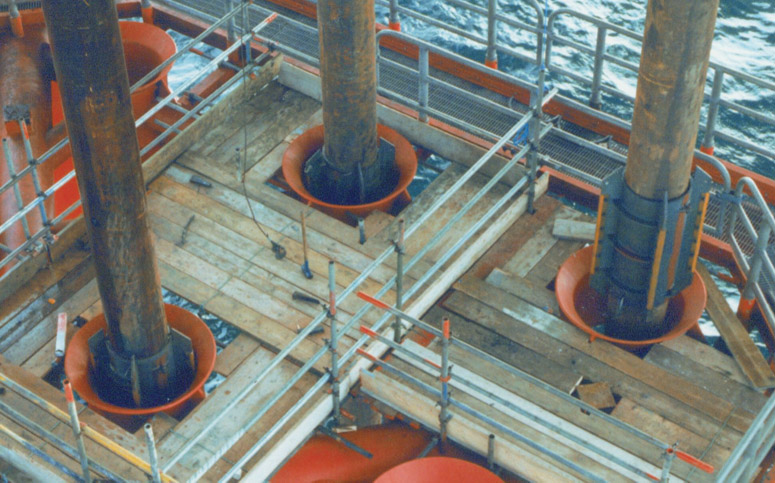
UWG Ltd provides a consulting engineering design, fabrication and
offshore service for the oil and gas industry. LUSAS Analyst
was used to carry out
detailed analyses of centraliser designs to investigate their ultimate strength and
fatigue life.
Oil from a sub-sea well is conducted to the surface through a set of
concentric tubes called risers. Centralisers are used to locate these risers in guides
that form part of the production platform support structure. Centralisers are subject to
lateral loads caused by wave action on the riser and may also undergo axial loading if the
centraliser catches on a guide during installation. Two types of centraliser
were examined. The Type l centraliser is bolted around the riser without clamping it and is
held in position by collars welded to the riser. The Type 2 device is bolted tight to the
riser and deforms to the riser pipe shape.
The Type l
centraliser was modelled using 3D shells with joint elements representing bolts. The
design wave load was applied radially along a single line on the inside of the
centraliser. Stresses were obtained for a number of different incident angles of design
wave loading and compared with material properties to assess the strength of the design. A
number of different designs are being investigated with variations in material thickness
and number and depth of stiffening rings. Stresses and forces due to axial loading are
currently being investigated and this is to be followed by an analysis of the stresses
induced in the riser. |
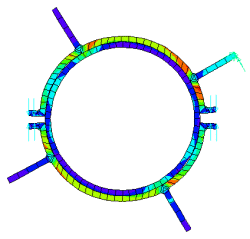
|
In the Type 2 centraliser a 2D nonlinear plane stress
model is being used prior to a full 3D analysis being carried-out. Use of the LUSAS
slideline facility simplifies modelling the contact between the centraliser body and the
riser. Bolt loadings to clamp the centraliser to the riser were applied iteratively and
the design wave loading was applied in a direction to give the highest stresses. A number
of different models have been used to investigate the effect of varying the
centralisers material thickness. Graphs of centraliser stress versus centraliser
thickness and riser stress versus centraliser thickness have been obtained and work is in
hand to check whether using a finer mesh affects results. Future work will extend the
model to include 3D effects.
Other LUSAS Analyst case
studies:
|