Case Study
LUSAS used to
prove nuclear safety case at Devonport Royal Dockyard
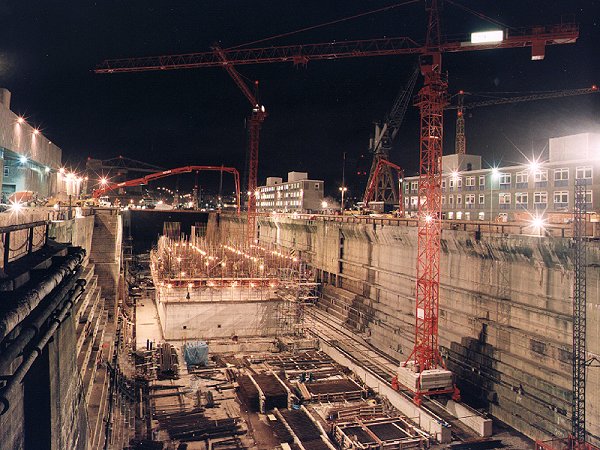
The Consultancy Services department at
LUSAS worked in partnership with Babtie Group on the nonlinear
dynamic analysis of a variety of major structures. The seismic qualification analysis
was
required as part of the multi-million pound modernisation programme of nuclear submarine
refit facilities for DML at Devonport Royal Dockyard.
As
part of the work, nonlinear dynamic analysis with LUSAS Civil &
Structural was carried out to predict the stability and structural integrity of
massive cellular, reinforced concrete caissons at numbers 9, 10, 14 and 15 docks during a severe
seismic event. These multi-celled gravity structures are used to seal-off the open ends of
dry-docks. After construction, each caisson is floated into place at the entrance of the dock, ballasted with
water, and sunk into position prior to the draining of the dock.
On number 15 dock caisson, a preliminary analysis of
caisson response using the prescribed seismic data led to the adoption of a full-width
0.3m deep shear-key and stop-block to restrain caisson movement. A further 9 analyses were
performed with a more detailed LUSAS model to give an initial assessment of the effect of
friction coefficient, foundation stiffness and ground acceleration upon both caisson
movement and internal forces and moments. Finally the LUSAS model was transferred to
Babtie Group for further sensitivity analysis runs.
|
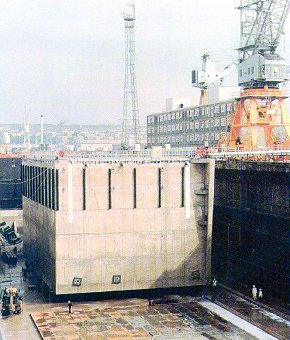
|
Modelling
The
caisson was idealised in LUSAS Civil & Structural by using 4-noded thin shell
elements for the cell walls and 4-noded thick-shell elements for the caisson base.
Nonlinear contact joint elements were used to model the lift-off and frictional sliding at
the foundation, stop-block and shear-key interfaces. Additional joint elements were used
to provide hydrodynamic mass and damping actions on the walls and base-interface
respectively.
Ground acceleration history from BNFL Engineering Ltd. for
a UK hard site provided the seismic input with increments of 0.005 second being used for
each time step. Hydrostatic pressure and self-weight were applied as initial static loads.
Hydrodynamic forces from the water enclosed in the cells were simulated by locating joint
elements at each node on each wall and assigning directional masses calculated using the
Westergaard model. Acceleration histories were applied to the foundation to drive the
ensuing dynamic analysis. Values of frictional damping at the contact interface of 3%;
structural damping of 5%; and interface damping of 2% to simulate the effect of the fluid
between the base and the dock floor were used in the analyses.
Results processing
After running the analyses, full use was made of the
extensive results processing features in LUSAS. Time-history plots were obtained showing
total reactions on the caisson base and reactions at the stop-block and shear-key.
Envelopes of maximum and minimum shear force and bending moment were obtained for each
caisson wall and the base for all 9 analyses. To assist with steel design, envelopes of
Clark-Nielsen forces were also produced for all of the walls. This method combines
in-plane and out-of-plane actions to derive the tensile force to be carried in the plane
of the steel. Time histories of displacement, velocity and acceleration were also produced
for all 8 corner nodes of the caisson. Secondary response spectra were obtained from these
motions for use by equipment designers. Animations of each simulation were created to give
a complete overview of the response of the caisson to the seismic event.
In Summary
Using the comprehensive results obtained with LUSAS Civil
& Structural, Babtie Group were able to prove a safety case for the caisson. The
analysis clearly demonstrated that the caisson had adequate structural capacity to
withstand a seismic event and that the seals could accomodate the displacements expected.
Independent technical assessment and peer review has been carried out by leading UK
nuclear engineering consultants who have accepted the use of LUSAS finite element analysis
for these advanced analyses in the nuclear industry.
Find out more
Other LUSAS Civil &
Structural case studies:
|
|
Software Information
|