Case Study
Share this
article
Cantilevered glass canopy, Tokyo
-
Novel laminated
glass and acrylic bladed structure
-
Linear static
self weight, thermal and wind loading assessment
-
Seismic analysis
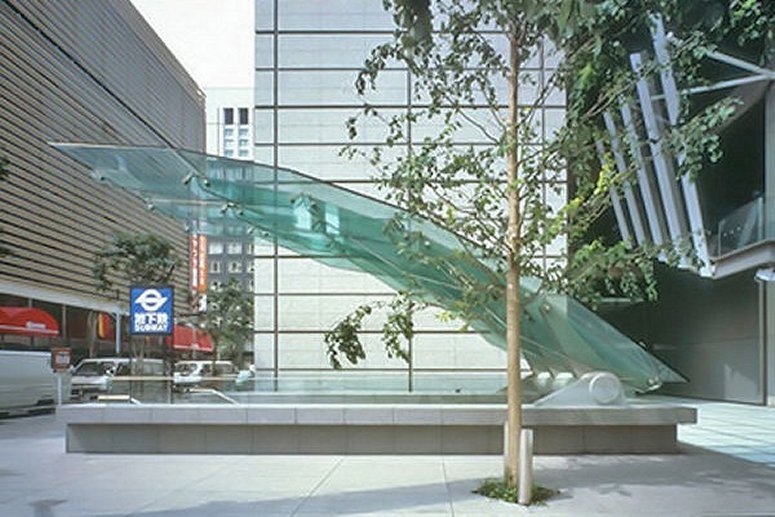
The plaza of Tokyo International Forum in Japan features a unique 10.6m
long cantilevered glass canopy designed by Dewhurst Macfarlane and Partners with the aid
of LUSAS Civil & Structural
The canopy shelters an 8m x 4.8m wide staircase well leading to the
Yurakucho underground station. The supporting structure comprises cantilevered beams each
made up of 4 component beams pinned at their middle and end points to form an arch. These
component beams are made up from both laminated glass and acrylic blades that reduce in
number from 4 blades at the base of the cantilever beam to 1 blade at the tip. The blades
are connected by 40mm diameter stainless steel pins to T-shaped brackets which in turn
support the glass panels forming the canopy roof. At the base of the canopy V-shaped
stainless steel brackets connect each cantilever to a horizontal beam running the full
width of the canopy.
LUSAS
Civil & Structural was used to investigate the response of the canopy to both
static and dynamic loadings. The effects of self weight, differential thermal effects, and
wind loading, both from the front and the rear of the structure were studied. Thin shell
elements were used to model the cantilever beam blades, roof panels and support brackets
with thick beam elements being used to model the base connections. Joint elements modelled
the connections between the glass blades and stainless steel pins. |
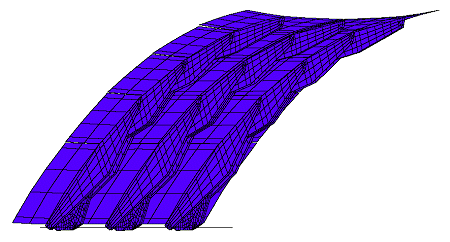 |
To assess the response of the canopy to seismic loading a natural
frequency analysis was done followed by two spectral response analyses using expected
local ground accelerations. Two different levels of structural damping were also allowed
for. Initial attempts to perform the natural frequency analysis revealed a large number of
mode shapes in the glass roof panels. This prevented extraction of the higher frequency
global modes which have a significant influence on overall response. To overcome this
problem, a useful procedure known as Guyan Reduction was used to filter out the low-energy
modes to leave only the dominant global modes in the solution.
By
using the extensive graphing, contouring and plotting features in LUSAS, structural
deflections, forces and moments in the joints, and stresses in the roof panels and
cantilever members were obtained to help optimise the design. The peak joint forces and
corresponding stresses from the seismic analysis were generally found to be greater from
the spectral response analysis than those from the static loadcases. This was mainly due
to the CQC values used applying ground accelerations in all 3 directions, inducing lateral
loads which were not applied to the static loadcases.
Tim Macfarlane, responsible for the design of the canopy was pleased
with the results obtained. He said: "By using LUSAS Civil & Structural
for this project we were able to determine with confidence the response of the structure
to earthquake loading and to check the analysis for wind and dead loads against more
conventional computer models and our preliminary hand analysis".
Since completion the canopy has already withstood two typhoons and an
earth tremor measuring 6 on the Richter scale. At the 1997 British Construction Industry
Awards, the Yurakucho canopy received a special commendation for demonstrating British
expertise in the design and construction of glass structures.
"By using LUSAS
Civil & Structural
for this project we were able to determine with confidence the response of the structure
to earthquake loading and to check the analysis for wind and dead loads against more
conventional computer models and our preliminary hand analysis".
Tim Macfarlane,
Partner, Dewhurst MacFarlane and Partners
Share this
article
Find out more
Other LUSAS Civil &
Structural case studies:
|