Case Study
Rail track/structure interaction
analysis for the Honam high speed railway
-
Rail track /
structure interaction analysis
-
Temperature,
acceleration and braking loads evaluated
-
Induced rail
stresses and track displacements all within design limits
Saman Engineering
Corporation is using LUSAS Bridge analysis software for
preliminary design work on the Honam high speed railway on behalf of
its client the Korea Rail Network Authority. As part of this work, a
rail track/structure interaction analysis has been carried out for a
1.8km long viaduct bridge structure, with a 3-span centre section of
steel box framed construction, that carries the railway over the
Mangyeong River near Iksan. Axial forces in the rails due to
acceleration and braking forces caused by passing trains were
evaluated and induced track displacements relative to the bridge deck
were checked and found to be within the specified design limits.
Overview
The Honam high speed railway, when
complete, will link South Korea’s capital city, Seoul, with Mokpo, a
southern port city in South Jeolla Province. It will be South Korea’s
second high speed railway. The first, the Seoul-Busan line, has been
in operation since 2002. The Mangyeong River crossing, one of many
structures on the new route, has a length of 1,875m and comprises a total
of 50 spans of varying length and construction type. Three steel box
framed spans of 60/75/60 metres over the river are flanked by steel
girders of 50m span, and then by various numbers of 35m and 30m
pre-stressed concrete box section spans for the remainder of the
crossing’s length.
Rail Track Analysis
To model the bridge Saman used the
LUSAS Rail Track Analysis option. This allows rail track/bridge
interaction analysis to be carried out to the International Union of
Railways Code UIC 774-3. It builds models automatically from data
defined in MS Excel spreadsheets, runs an analysis, and produces
results in spreadsheet or LUSAS formats. To do this, the bridge is
simplified and ‘broken-down’ into beam elements which represent
the track and any supporting structure, with nonlinear springs being
used to model the ballast and expansion joints. Bearings and
foundations are modelled
with simple springs. Temperature change in the rails and structure,
and train loadings from acceleration and braking forces must also be
defined. Changes in temperature and the passage of trains on different
tracks accelerating or braking across the structure induce axial
compressive forces in the rails and displacements in the rails
relative to the bridge deck. These needed to be evaluated to ensure
that they remain below specified design values for all in-service
situations.
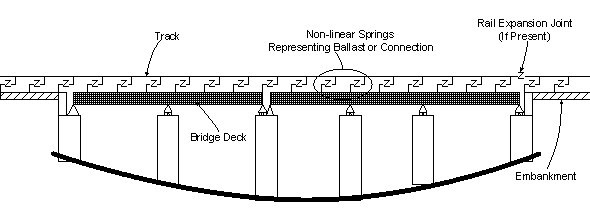
The UIC 773-3
Structural System
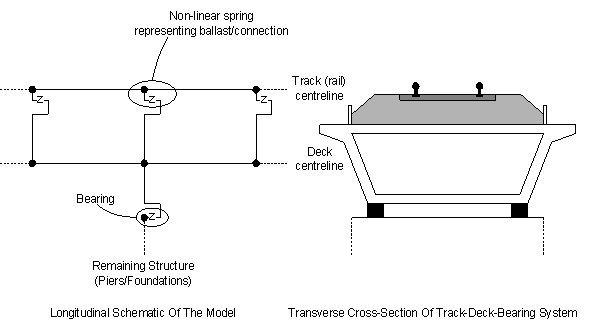
UIC 773-3
Track/Deck Modelling
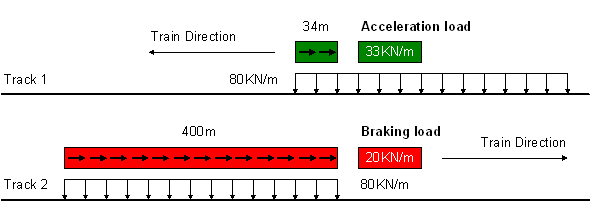
Typical train loading
configuration
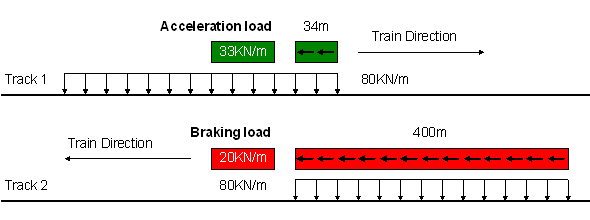
Typical train loading
configuration reversed
Modelling and
Analysis
For the Mangyeong River crossing,
Saman created two LUSAS models to investigate the response of the
structure. In one, automatically generated by the rail track analysis
option, single beam elements modelled the deck and all spans of the
structure. In the other, the initial rail track analysis-generated
beam model was additionally edited in LUSAS to include the 3-span
framed steel box members and included appropriate geometric and
material properties for the added features. This somewhat unique
method of increasing the accuracy of the UIC code analysis
subsequently proved to be of real benefit when the results from both
modelling methods were compared.
Results
From the results obtained from the
LUSAS rail track analysis Saman created graphs for both the simple
model (using beams only) and the full model (which additionally
modelled the framed steel members). These showed the variation of
axial compressive stress in the rails as a result of the temperature
and acceleration / braking loading. From these graphs it was seen that
full modelling of the steel framed members produced a reduced axial
compressive stress in the track over that shown for the simple beam
only model - reassuring Saman in its design.
Mr Jeongil Kim, Assistant Senior
Engineer in Saman Engineering's Railway Structures Department said: "Correct modelling of the nonlinear behavior of ballast,
and of the interaction between the ballast and the rail track is not
easy to do manually, so the LUSAS Rail Track analysis option, which
handles this automatically, was very useful to us in this
respect". He continues: "The easy use of the rail
track analysis option was a key benefit on this project. Even though the
model was built automatically we could still modify it for our own use
without it ruining the original model".
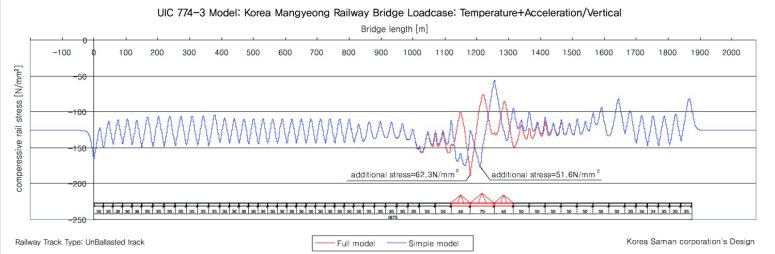
Compressive
stress in the rails from temperature and acceleration loading for
both simple (beam only) and full (including framed steel members)
models
(click for larger image)
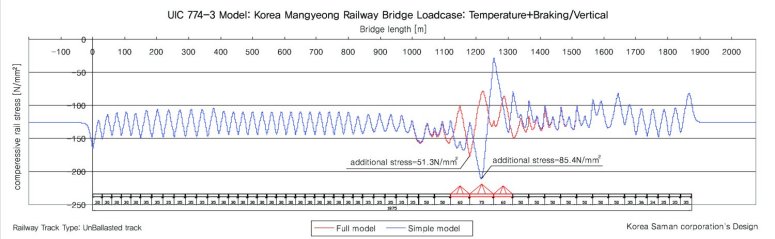
Compressive stress in
the rails from temperature and braking loading for
both simple (beam only) and full (including framed steel members)
models
(click for larger image)
"Correct modelling of the
nonlinear behaviour of ballast, and of the interaction between the
ballast and the rail track is not easy to do manually, so the LUSAS
Rail Track analysis option, which handles this automatically, was very
useful to us in this respect".
Mr Jeongil
Kim, Engineering Manager, Saman Engineering
Find out more
Other LUSAS Bridge case studies:
|