Case Study
Design of the Novi
Sad Friendship Bridge
- cable stayed swing footbridge
- global analyses of structure
- local analyses of critical components
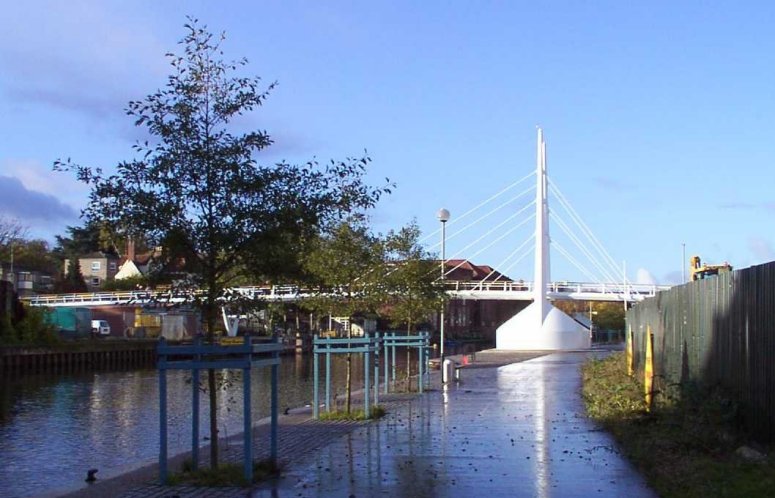
Novi Sad Friendship Bridge is an asymmetric cable stayed swing
footbridge which spans the River Wensum in Norwich to provide access to a new commercial
development and helps regenerate a historic but run-down part of the city. The
structure is named in recognition of the twinning ties between Norwich and Novi Sad in
Serbia. Buro Happold Consulting Engineers Ltd
in association with architects, Yee Associates, used LUSAS Bridge to generate
global and local models of the steel superstructure to assist with the design and analysis
of the crossing. Norfolk County Council were co-consultants on the project.
The bridge carries a footway/cycleway and comprises two approach spans of 5m and 14m on
the eastern bank, a 28m central span which swings about the main tower and a 5m span on
the western bank. The main bridge is cable stayed and it is also supported through a steel
shroud, beneath which the rotating machinery is housed. The deck cross section is made of
two main 400mm by 400mm rolled sections, rotated at 45 degrees to give a diamond shaped
beam. The deck consists of a 10mm plate spanning between the main beams, with transverse
ribs at 2m centres and with longitudinal stiffeners to reduce the local deflections.

According
to Karim Yngstrom, the nature of the structure made the global analysis quite challenging.
He said, 'The asymmetric layout of the cable stayed spans required kentledge on the
shorter (back) span to counteract the overturning moment arising from the self weight of
the main span. The initial design had considered using a thick steel plate but this was
abandoned as it required relatively thick (113mm) plates and increased the overall weight
of the structure considerably. The final solution adopted was to provide a permanent steel
shutter under the deck plate filled with steel ingots'.
To investigate the response of the structure three separate
global models were created in LUSAS. The first was used to determine the behaviour of the
bridge under dead load where the structure is in effect three different structures
with the east and west ramps and the main swing bridge behaving independently from each
other.
The second model was identical to that used for the dead load analysis,
but was subject to displacement loading at the interface between the ramps and the swing
bridge. The results of this analysis allowed Buro Happold to determine the additional
stresses arising from possible mismatch caused by the effects of temperature, high uplift
wind and snow loading. |
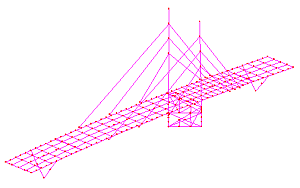
|
|
|
The third model represented the structure at its operational condition
where the edge beams provide continuous shear transfer along the structure through a
connecting pin between the ramps and the main bridge. The joining pins were modelled with
their true degrees of freedom allowing only vertical force transfer between the ramps and
the main bridge.
The results from each analysis were then combined and
enveloped in separate spreadsheets and the maximum load effects for each member were
determined.
The deck anchorage detail
and the steel shroud to the tower were singled out for more detailed investigation with
LUSAS. Local models of these critical regions were generated and in-service stresses and
displacements were obtained. Stresses due to local effects at other members were
calculated from first principles. As Karim explains: 'Using LUSAS
was the only viable way of analysing the structure for the multitude
of loadcases that had to be considered - in effect, we couldn't have
done it any other way'.
|
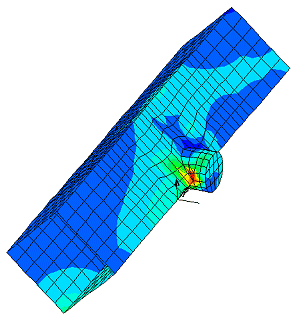
|
"Using LUSAS
was the only viable way of analysing the structure for the multitude
of loadcases that had to be considered - in effect, we couldn't have
done it any other way."
Karim Yngstrom, Buro Happold
Find out more
Other LUSAS Bridge case studies:
|