Case
Study
Pier
Design on the Plashet School Footbridge
- steel plate bridge pier
- eigenvalue buckling analysis
- optimised design
A 67m long footbridge links the two sides of Plashet School across
Plashet Grove in Newham, London. Designed by structural engineers Techniker with architects Birds Portchmouth Russum
for Newham Borough Council it is supported on sculptural steel piers that emerge as
distorted fins from the ground and clamp the bridge on either side. According to
Techniker, the sculptural expression of the piers begged to be formed from a single sheet
of steel. LUSAS Bridge was used to verify the initial design assumptions and to
try to reduce the plate thickness to justify the elimination of stiffeners.
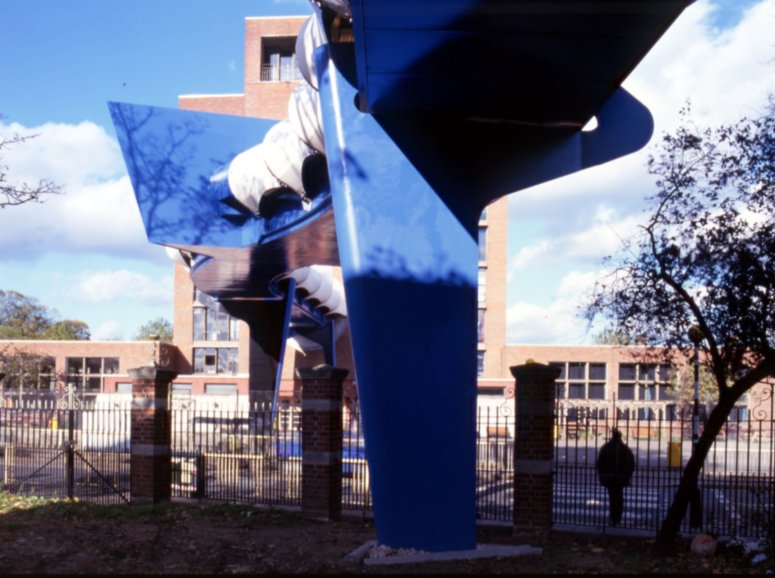
Cost was the main driving force behind
the final design, against which the appearance needed to be balanced. The options studied
included solid steel plate, diaphragms, and as a compromise to examine the real cost
difference - folded and stiffened plates. A diaphragm was quickly discarded as the cost of
fabrication outweighed the saving in steelwork. The initial design suggested an
unstiffened plate thickness of 40mm against which the integration of stiffeners into the
design needed to be balanced.
A full 3D model of the pier structure was generated
using 3D thick shell elements. A refined mesh was used at the pier base and around the top
and also for the site-welded connection plates where the stress distribution was expected
to be critical. Reactions for five different loadcases were derived from a linear
bridge deck analysis. A crash load of 50kN was applied horizontally to the pier as a
globally distributed line load, 3.0 m above ground level. The S-plan form of the bridge
generates twist which needs to be taken out at the supports. Additional horizontal loads
were applied to the connection plate surfaces to account for the construction tolerances
and the thermal expansion of the bridge deck of +/- 50 mm in the transverse and
longitudinal directions.
Two eigenvalue analyses were performed to extract the
natural frequencies and the buckling load factors of the structure. Solutions for the
first five modes were obtained using Subspace Jacobi Iterations. Close examination of the
results and tweaking of the model to smooth out hot spots allowed Techniker to reduce
the steel plate thickness to 32mm, thereby justifying the elimination of stiffeners.
The use of LUSAS Bridge on this project made it
possible to create a unique piece of sculptural steelwork within a very tight budget.
Find out more
|