Additional Information
See the adjacent Software Information
links for general details regarding LUSAS Bridge software products and
options.
Prestress / Post-tensioning
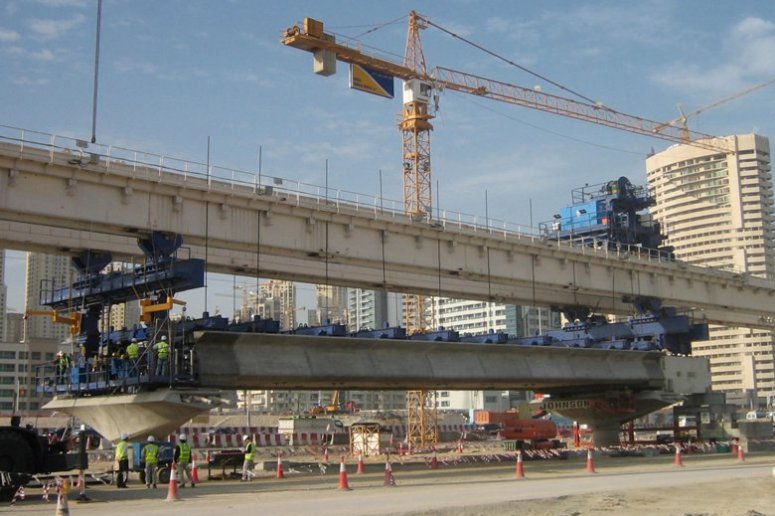
Prestress / Post-tensioning in LUSAS is
suitable for beams, slabs and volumes, and incorporates time-stage
with creep and shrinkage. Span-by-span, progressive placement
(segmental), balanced cantilever and incremental launching time staged construction methods are
supported. Use
the post-tensioned bridge wizard to generate
a box girder as constructed by the "Free Cantilever Method"
- LUSAS calculates equivalent nodal loading due
to any tendon prestressing or post-tensioning and assigns these forces
automatically to beam, shell, or solid elements of a model
for a chosen loadcase or set of loadcases.
- Computation of tendon forces can
be carried out in accordance with supported design codes.
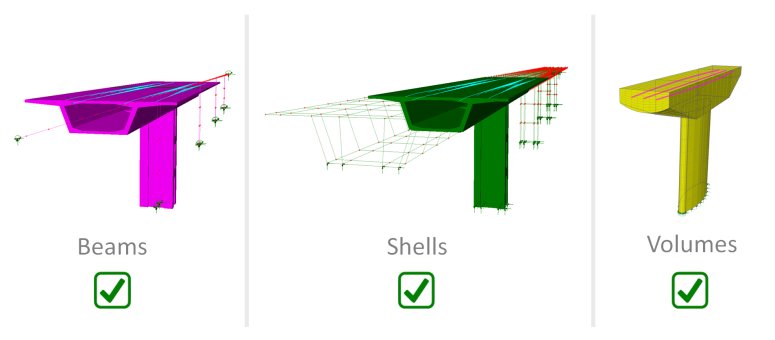
|
Beam (line),
shell (surface) and solid (volume) modelling of concrete is
supported. |
Tendon
definition and modelling
Define tendon profiles and
view the developing tendon shape in real-time as it is being defined,
or copy and paste data from a spreadsheet. Tendons can also be
generated by selecting lines, arcs or splines that are defined
or imported into LUSAS Modeller. Manual definition by
coordinates in 3D space or by defining coordinates in two
2D planes is supported. Locally defined tendon profiles can be used
anywhere in the model and any number of times.
Define tendon
properties and values/settings relating to instantaneous and
time-dependent losses. All other values required in order to carry out
calculations of prestress losses in accordance with the design code
are obtained directly from the model. Elastic
shortening due to stressing of other tendons according to the selected
design code or user-defined percentage losses is taken into effect.
Time dependent effects can also be considered.
Supported design
codes which include time dependent effects
for any stage of construction are:
- AASHTO LRFD 5th to 9th Edition
- CEB-FIP Model Code 1990
- EN 1992-1-1:2004 / 2014 Eurocode
- fib Model Code 2010
- IRC:112-2011
- JTG 3362-2018
Supported design
codes which exclude time dependent effects, only producing results for short term and long term losses
are:
- AASHTO
LRFD 2nd Edition
- AASHTO
LRFD 5th to 7th Edition
- BS5400-4:1990
- DD
EN1992-1-1:1992 Eurocode 2
- EN
1992-1-1:2004 /2014 Eurocode 2
- JTG
D62-2004
LUSAS calculates losses appropriate to the age of the concrete and the magnitude and duration
of prestress and other loading at any selected time typically at each
stage, and at the end of the service life of the structure. Depending
upon the design code these loss calculations may be:
-
Based on time
inputs and calculated stresses, which allow for producing details
and results of losses at any time and for any stage of
construction.
-
Approximate,
requiring input of estimated stresses, which allow for producing
details and results of short term and long term losses only.
For design codes that
support time-dependent loss calculations, adjustment of losses to
account for prior losses are also calculated.
Simply assign the
tendon loading (which associates a tendon profile and a tendon
property with a specified prestress force and associated jacking
and loss details) by dragging and dropping it onto selected line, surface or volume features in a
model for a single or a range of loadcases. When solving a
model, LUSAS
calculates equivalent nodal loading from the assigned prestress tendon
loads and assigns these forces automatically to those features
(and hence nodes and elements) of the model for a specified loadcase.
Discrete loads and the applied forces / moments calculated can be
viewed for checking purposes.
View primary and secondary load effects arising from prestressing, and primary effects from each tendon loss type (friction, anchorage, elastic shortening, creep, shrinkage and relaxation).
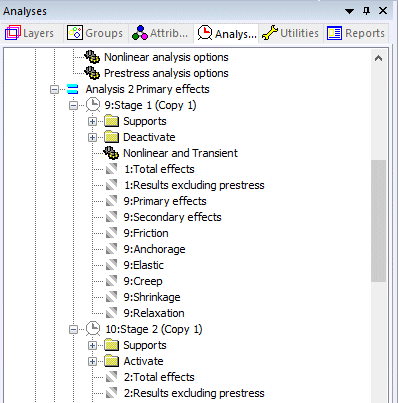
Produce graphs of
tendon prestress force after time-dependent losses.
Add tendon properties, profile, loading, losses and setting-out data
for all tendons assigned to a model to a model report.
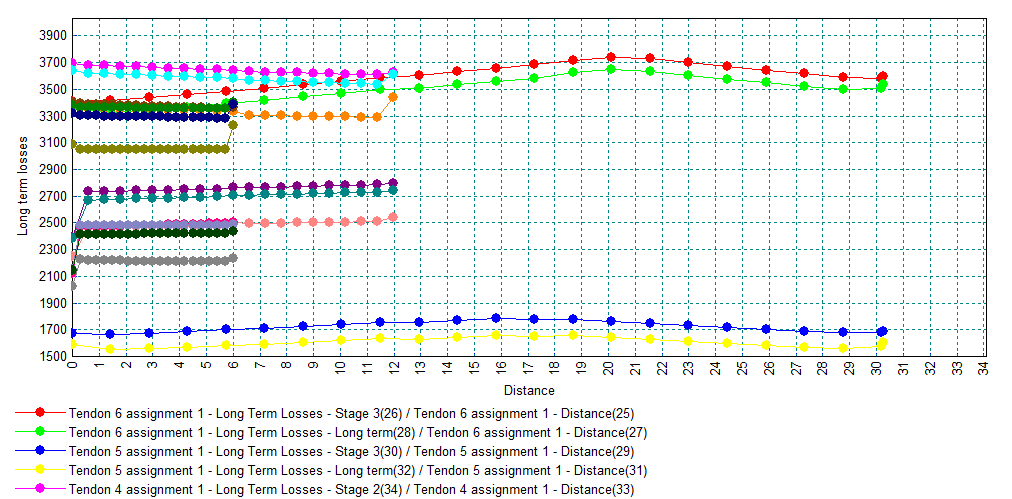
|
Typical graph
showing reduction in prestress force after time-dependent losses |
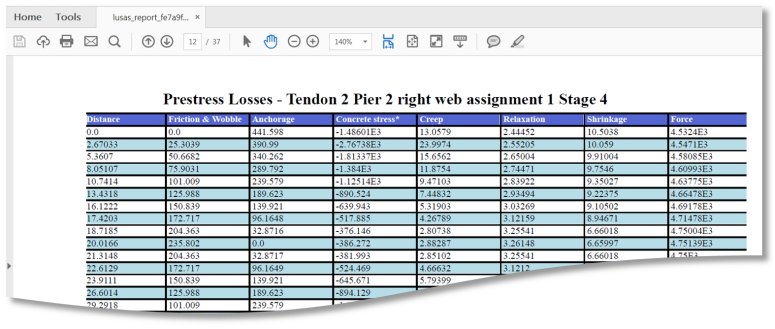
|
Produce reports
of tendon properties, profile, loading, losses and setting-out
data for all or selected tendons. |
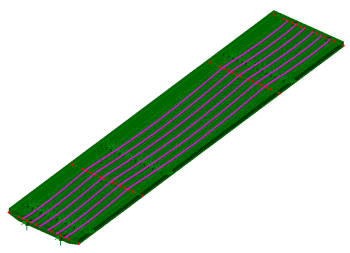
|
|
Post-tensioned
bridge slab deck |
External tendon
modelling
For modelling
external tendons as, for example, where external tendons are
included between deflector plates in a structure, the tendons
can be incorporated into the model as bar/
beam elements with applied forces, and typically requires shell or solid elements to be used to model
the structure. Modelled in this way, the
true behaviour of tendons due to the compression of the
concrete is obtained. Alternatively, equivalent load methods
could also be used. |
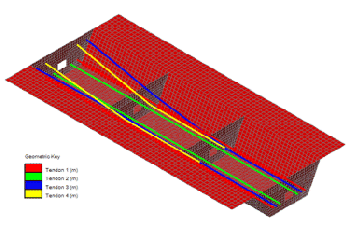
|
Time stage construction
All types of time staged
construction methods can
be used in conjunction with the post-tensioning facility. See
the staged
construction analysis information page for more details.
Post-tensioned
Bridge Wizard
-
Generate a beam model of a box girder as constructed by the "Free Cantilever Method" in a fraction of the time taken by manual methods.
-
Automatically model the entire construction sequence in order for a step-by-step nonlinear analysis incorporating concrete creep and shrinkage materials (and age attributes) and tendon loading including time dependent losses to be carried out.
Easy to define
From basic setting out data, segment dimensions, construction times and concrete ages, the FCM wizard creates the necessary tendon loading attributes and assigns each to the correct segments at each stage of construction, considerably speeding-up the modelling process.
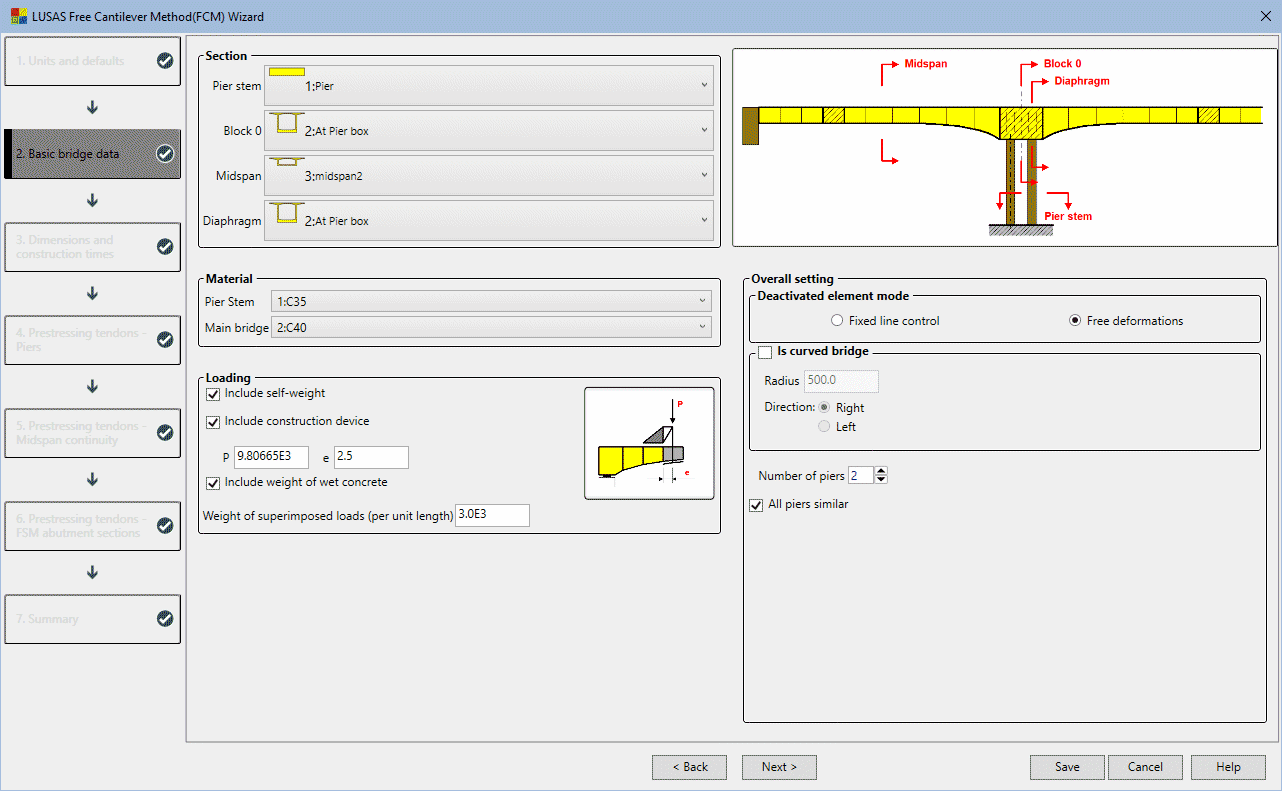
Dynamic
visualisation of tendons
Dynamic visualisation of tendons in the
bridge on plan, elevation and within each segment section is provided,
showing the segment installation sequence for each selected
construction stage, along with tendon setting out data.
Tendon profiles suitable for balanced
cantilever box girder-type bridges constructed by the Free Cantilever
Method are used (with FSM used at end spans adjacent to the
abutments). Tendons are categorised into five types, with setting out
details for each provided on the relevant prestressing tendon input
pages of the FCM wizard.
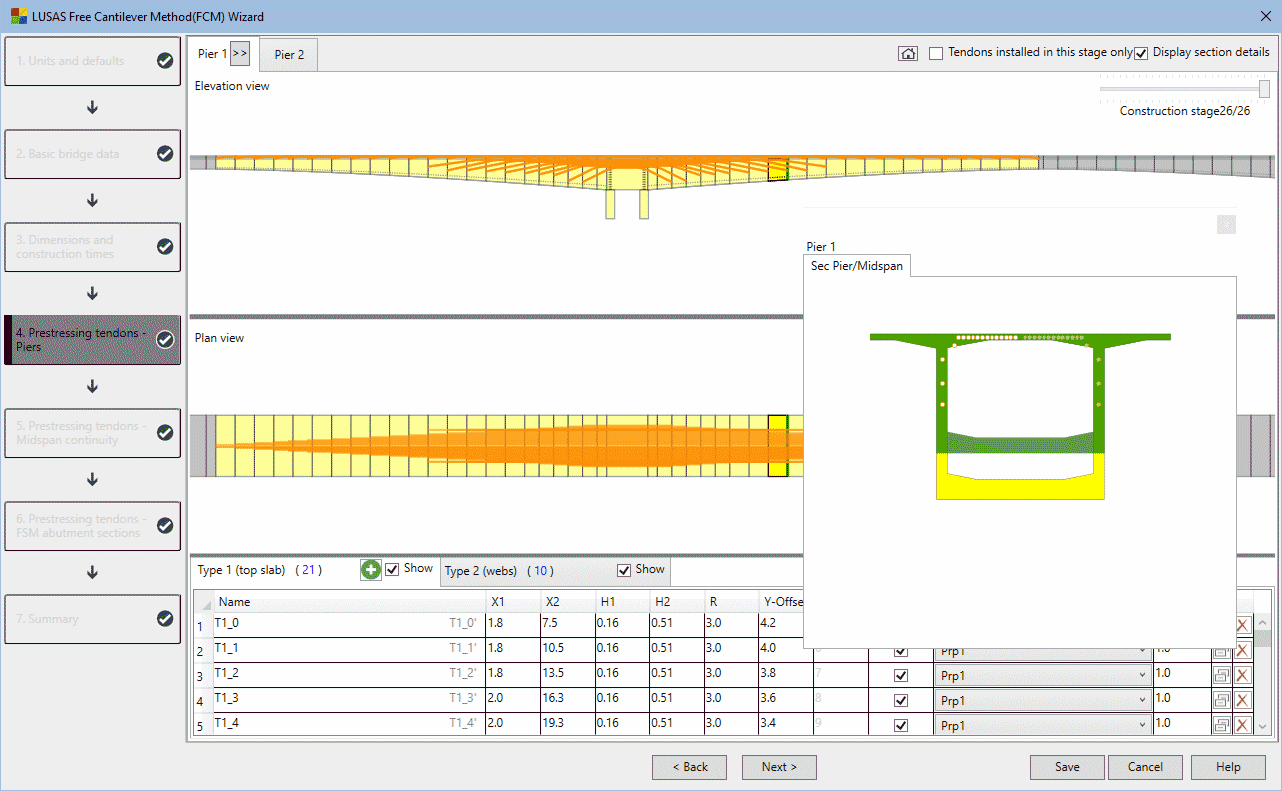
Check before you
build
A summary dialog shows segment length,
construction times and age of segments for each selected construction
stage, allowing for easy validation of inputs, and detection of errors
prior to building a model.
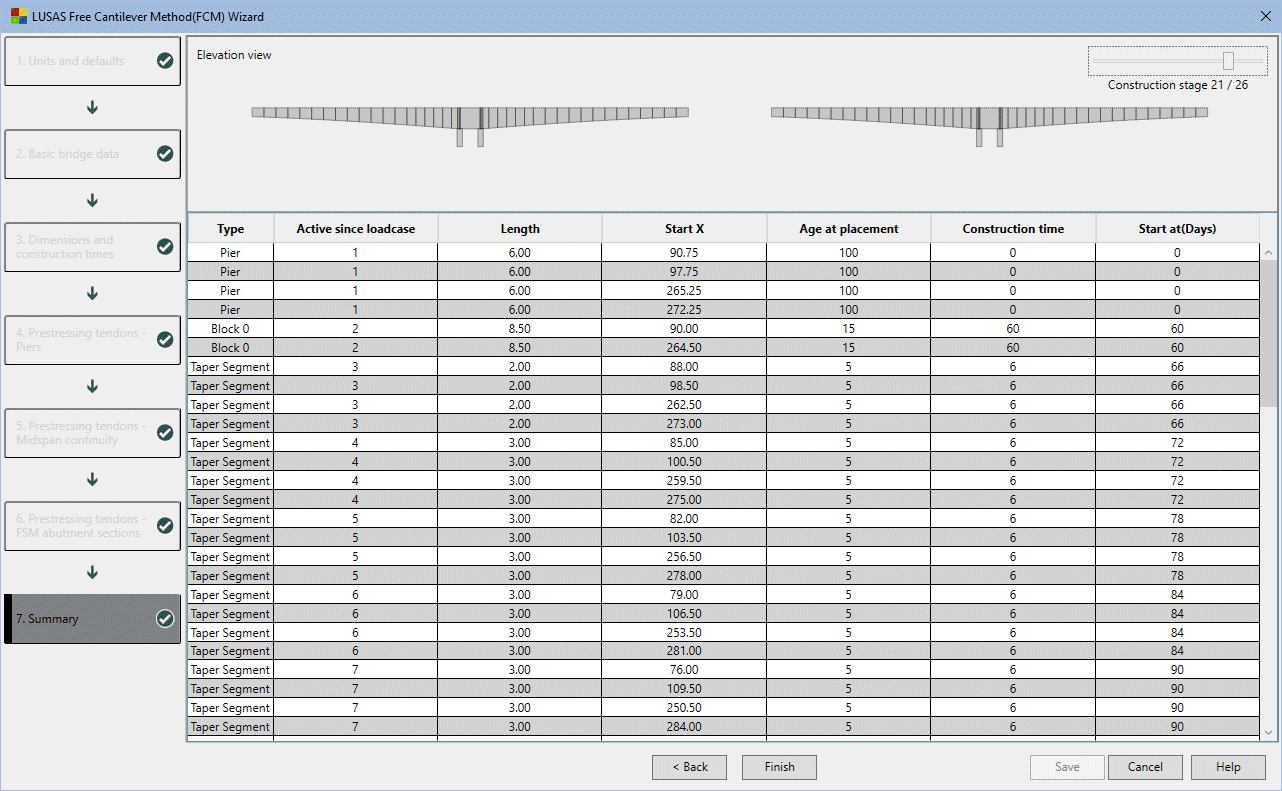
Once complete, a model capable of
modelling the entire construction sequence is built at the press of a
button, and on solving a model, tendon losses are calculated to a
chosen code of practice.
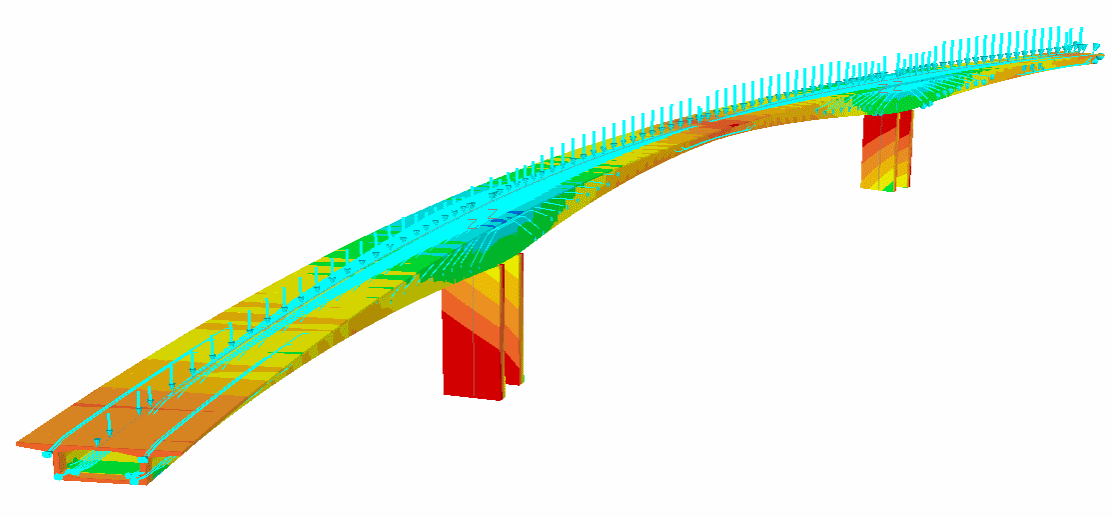
Bridge
feature / Capability |
Provided
by the Wizard? |
Straight or curved decks of constant radius. |
YES |
Box girder sections with vertical webs. |
YES |
Any number of spans and supports. |
YES |
Split piers with diaphragms. |
YES |
Tendon types commonly used in FCM bridges |
YES |
User-defined
tendon profiles. |
YES |
|