Case Study
Assessment of the Forsmo Bridge
- Steel truss arch railway bridge requiring upgrading for increased axle
loading
- Iterative model development to incorporate strain gauge results
- Global and local modelling to assess Ultimate, Servicibility and
Fatigue Limit States
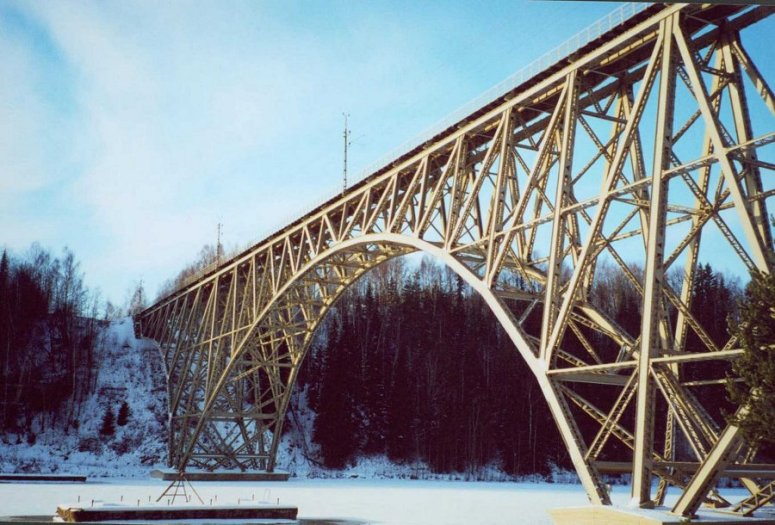
The use of on-site measurements to refine and improve an initial finite
element model of a structure for subsequent detailed analytical investigations is
invaluable. Ramboll successfully used strain gauge measurements on the Forsmo Bridge in Sweden to fine-tune a
LUSAS Bridge model prior to carrying-out an in-depth assessment of the structure
for a proposed increase in freight train axle loading.
Overview
Built in 1912, the Forsmo Bridge is a 263m long, 50m high riveted
steel-truss-arch railway bridge which crosses the Aangermann River in Northern Sweden
between Luleaa and Borlange. The 104m main span is linked by hinges to two side spans. As
part of the Swedish National Rail Administrations
STAX 25 programme the bridge was to be assessed and potentially upgraded for freight
trains with a 25 tonne axle load.
Modelling
A 3D model of the structure was built in
LUSAS to look at the effects of global deformation, the interaction between the main
arch-truss structure and upper superstructure which consists of braced longitudinal and
cross beams, and the distribution of sectional forces primary and secondary members. In
addition, a number of joints of particular interest were individually modelled in LUSAS to
derive stiffnesses and show local effects.
In the global model beam elements
represented all bridge members and because of this the derivation of centres of gravity of
the beams, beam eccentricities and stiffnesses of complex joints was of prime importance
in order to give valid results. Because of the difficulty in determining appropriate
values for modelling purposes strain gauges were used to help fine-tune the model.
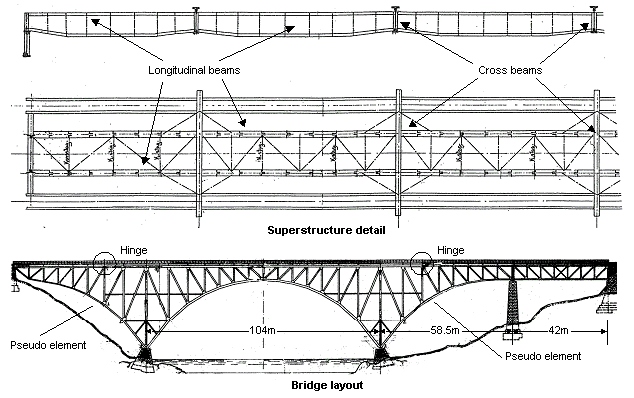
Strain gauge measurements
Bridges of this type are highly sensitive to the distribution of
sectional forces in the Ultimate Limit State and Fatigue Limit States. In recoginition of
this, the Swedish Rules For Classification Handbook recommends full 3D finite element
modelling and updating of models using on-site strain-gauge measurements. On the Forsmo
Bridge, groups of strain gauges were installed in carefully selected locations to obtain
information concerning the behaviour of the structure under in-service loading. From
these, time-series results from standard freight trains of known configurations and axle
weights were obtained.
By
plotting strain gauge measurements alongside corresponding results from the LUSAS model an
initial assessment could be made. Sensitivity analyses carried out using refined geometric
data and joint conditions then derived an improved model for re-assessment. This process
was repeated using a succession of updated models until the best possible overall LUSAS
model was obtained. The results obtained from updating of the initial model can best be
summarised by stating that the interaction between global and local effects proved to be
substantial with stresses in some members changing by more than 100% from their initial
values. This highlighted the importance of using this method.
|
|
Assessment results
The primary superstructure (consisting of members such as verticals,
diagonals and arch members) was found to have sufficient capacity for a 30 tonne axle load
and a corresponding distributed load of 100 kN/m with respect to Ultimate Limit State and
Servicibility Limit State. Both of these capacities are higher than that required by the
STAX 25 programme. With respect to the Fatigue Limit State the stress ranges for the most
critical members and riveted connections were all in accordance with the Swedish Rules for
Classification Handbook meaning that this part of the structure at least has the capacity
to be updated to modern train load levels.
|
For
the upper superstructure (consisting of longitudinal and cross beams) the analyses showed
that the ULS capacity could be upgraded to the 25 tonne axle loading required by the STAX
25 programme provided that yielding was allowed at selected joints to allow sectional
forces to be re-distributed. To try and achieve this various potential modifications to
the existing structure were assessed and nonlinear models of key joints were built and
analysed in LUSAS to aid with the assessment.
Ultimately it was shown that with respect to the Fatigue Limit State, an
upgrading of the upper superstructure for 25 tonne axle loads was possible provided that
the structure was modified to include extra bearings and modified joints. However, in
doing so, it would only have been possible to obtain a formal fatigue lifetime of 10-30
years. Because of this, a total replacement of the upper superstructure with new
longitudinal and cross beams is to be carried out instead. This will then allow for 30
tonne axle loads and give a service lifetime of 100 years. |
Updating of FE models and the benefits obtained
Ramboll
and the Swedish
National Rail Administration state in a published paper on the
Forsmo Bridge: Assessment results in the Ultimate Limit State and especially in the
Fatigue Limit State are very sensitive to precise finite element modelling and as such it
is not possible to assess bridge types like the Forsmo Bridge with sufficient precision
without updating a finite element model using on-site measured data.
"The combination of detailed and comprehensive finite element
modelling using LUSAS, sensitivity analysis, on-site measurements and updating of the
model has been proven to be essential to obtain accurate results. Once an exact model is
obtained, more advanced assessments such as plastic analyses, fracture mechanical
analysis, or probability-based safety analyses can be carried out with a far greater
degree of confidence".
Find out more
Other LUSAS Bridge case studies:
|