Case Study
Deck segment analysis for Yi Sun-sin Bridge
-
4th longest
suspension bridge in the world
-
Linear
static analysis of twin box steel deck segments
-
Diaphragm
design strengthened and optimised
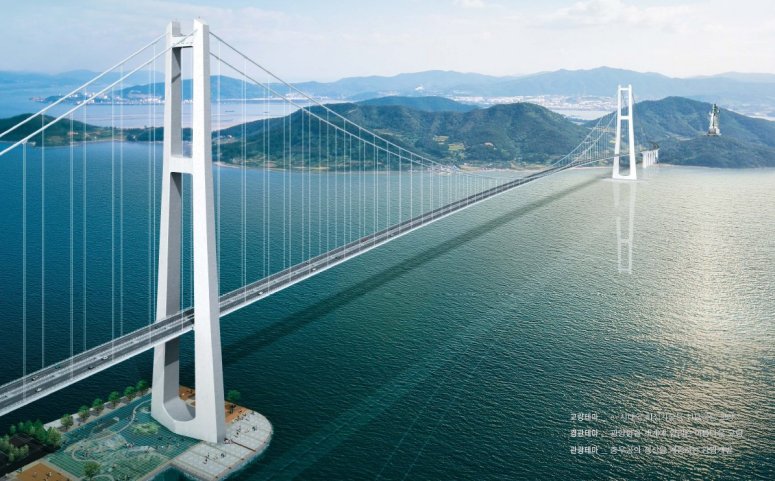
Yooshin
Engineering Corporation
used LUSAS Bridge analysis software to carry out a detailed analysis of a
6 metre long twin-box steel girder deck segment for use on the Yi
Sun-sin Bridge in Yeosu City,
Cheonnam, South Korea on behalf of its client the Cheonnam Provincial
Government. The bridge links Gwangyang to Yeosu city. The bridge is named in
honour of a famous Korean sea hero, Admiral Yi Sun-sin, an enormous
statue of whom will overlook the bridge. He was born in 1545 and
which, by deliberate design, is also the length of the main span of
the bridge in metres
Overview
The
bridge is a three-span suspension bridge of 357.5 + 1545 +
357.5 metre spans which, at a total of 2260 metres in length, and when
completed will be the fourth longest in the world. Concrete towers are H-shaped and at a
height of 270 metres are the highest in the world. The height from sea
level to the underside of the deck is in the order of 85 metres to
allow for the largest container ships in the world to pass safely
beneath the bridge. Preliminary design commenced in 2006 with detailed
design work taking place throughout 2007. Understanding how the twin
box girder deck section would behave under all loading conditions was
difficult to ascertain so LUSAS Bridge analysis software was chosen to
carry out a detailed analysis.
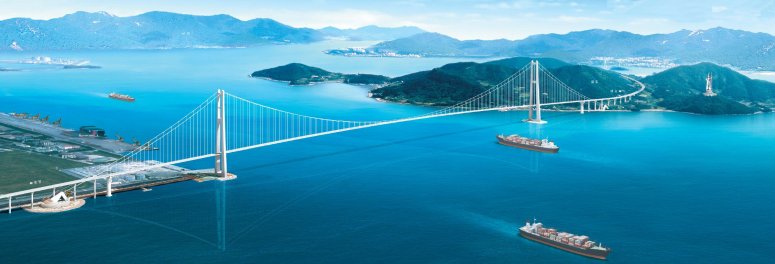
Modelling and Analysis
Using LUSAS, all webs, flanges, ribs
and other small members in the 6 metre long deck segment were
modelled. Vertical supports were placed at the hanger positions, and
moment supports were placed along edges where deck sections would join
to ensure the localised model would correctly match the global
behaviour of the bridge.
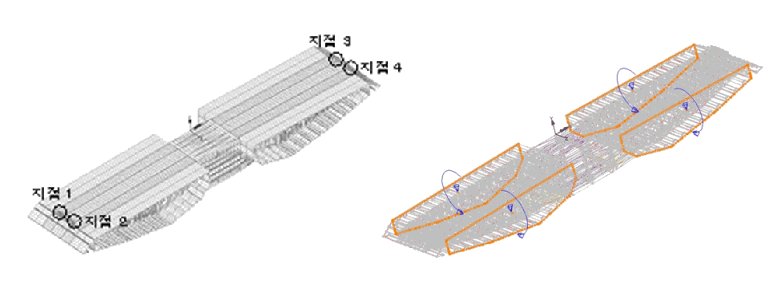
Four-lane Korean DB24
truck loading was applied as well as lane and distributed loadings,
and a linear static analysis was carried out. In all, 6 load
combinations consisting of 24 different vehicle loadings and dead
loads were analysed and investigated using the range of results
processing facilities available.

Slice sections through the diaphragm
were taken in areas of interest and both principal stress and
von-Mises stress were compared with the allowable stress for the SM490
steel members of the diaphragm and transverse box. From the detailed
LUSAS analysis it was seen that the main structural behaviour was in
the transverse direction, and, as result, it was seen that the initial
diaphragm design needed to be strengthened. Typical results plots
follow:
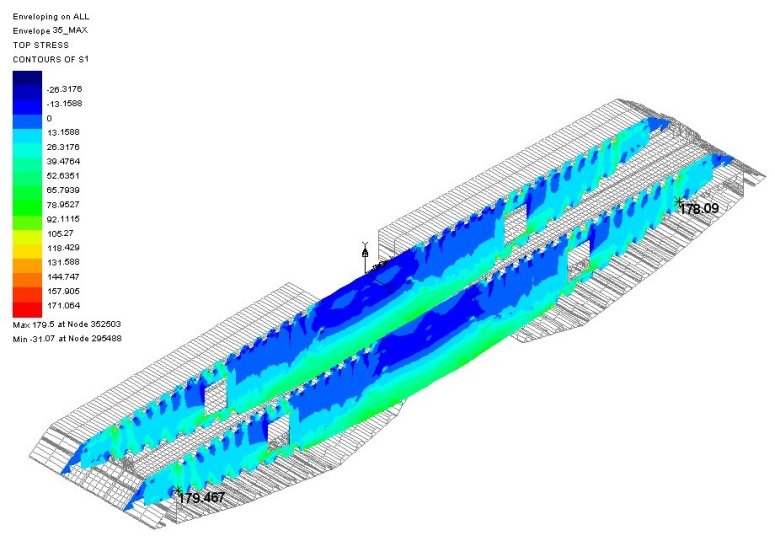
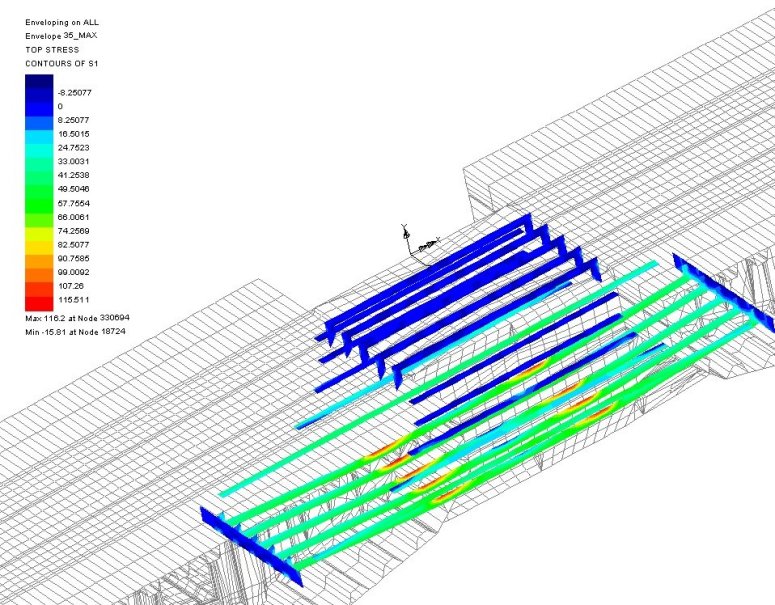

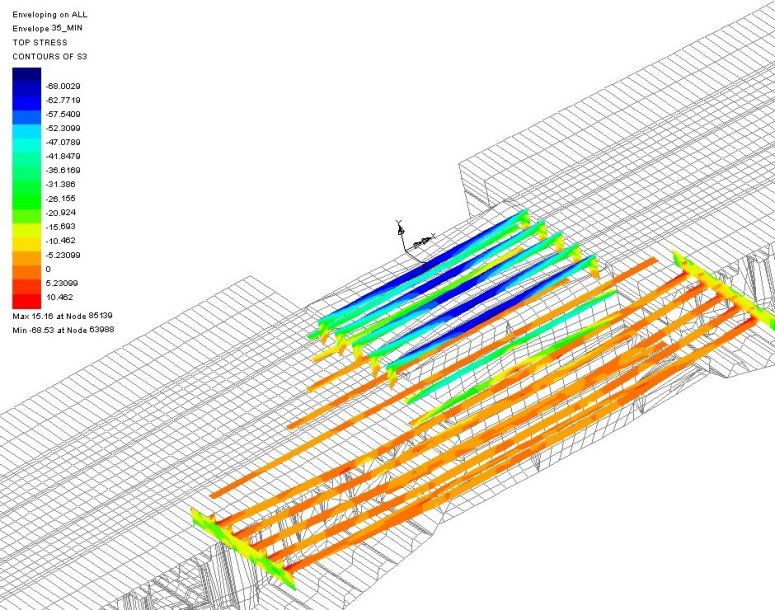
Construction of the bridge started at
the end of 2007 and completion is scheduled for early 2012. Total
project cost is in the region of 434 billion Won.
Find out more
Other LUSAS Bridge case studies:
|