Case Study
Cost-Effective
Steel Girder Rail Bridge Assessment
- steel girder rail bridge
- buckling assessment for 40 tonne lorries
- strength of structure proved by LUSAS
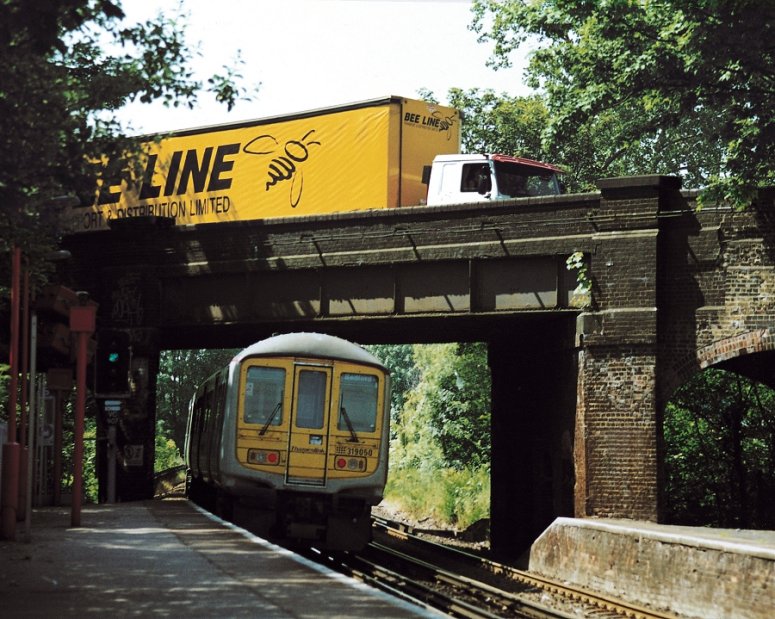
All bridges in the UK needed assessing for a 40 tonne weight limit in
order to meet new European legislation. As part of its bridge assessment program Railtrack
plc required a 3 span skewed structure at London Road, Hackbridge, London to be assessed.
Many steel bridges have been shown to fail assessment to design code
BS5400 Part 3. Two consulting firms, both using LUSAS Bridge have proved a 40 tonne
capacity on a structure that, according to the code, had insufficient lateral restraint
and would have required a severe weight restriction.
The bridge carries the A237 across 2 railway lines south of Hackbridge station and
consists of 2 brick arch approach spans and a central 12m span comprising steel edge
girders. These girders support brick parapets and main steel troughing spanning between
the masonry piers and onto their bottom flanges. An initial simple assessment identified a
possible deficiency and, following discussion with Railtrack reviewing engineer Pell
Frischmann, a more rigorous analysis was commissioned.
By using LUSAS Bridge, Robert West Consulting built a model of an
edge girder. In a straightforward modelling approach, QSL8 shell elements, which take
account of both membrane and flexural deformations and allow for eigenvalue extraction as
required for the buckling analysis, were used to model the web and flanges of the girder.
BSL3 beam elements modelled the flange to web angle connections and transverse web
stiffeners. A 40 tonne deck assessment analysis provided the vertical loading for the
girder and was applied as a series of increasing point loads to simulate the triangular
loading of the deck troughing. A UDL represented the self weight of the girder together
with the parapet load supported by the top flange.
In the eigenvalue buckling analysis the first 7 fundamental buckling
modes (or eigenmodes) were investigated. The eigenvalues or load factors obtained were
then applied to the initial analysis model to obtain the stresses in the top flange just
prior to buckling. These stresses were then used to determine the limiting compressive
stress at the critical buckling stage in the top flange in accordance with BS 5400 Part 3
Cl. 9.7.5. Additional calculations to confirm the stability of the girder under a lateral
overturning moment and sliding force were carried out in accordance with Cl. 9.12.4 of the
code.
In performing the category 3 check on the bridge
Design and Building Services of Sheffield City Council, who perform numerous bridge
assessments of this type, adopted a slightly more detailed modelling approach. QTS4 thick
shell elements were used for all parts of the edge beam girder including the web
stiffeners. By using rigid supports at abutments, spring supports at the position of
transverse edge beams and a slightly finer mesh it was shown that the edge beams had
adequate strength, confirming the original bridge assessment. A minimum load factor of
2.55 was obtained indicating that using spring supports to model the restraint provided by
the deck and stiffeners can be significant.
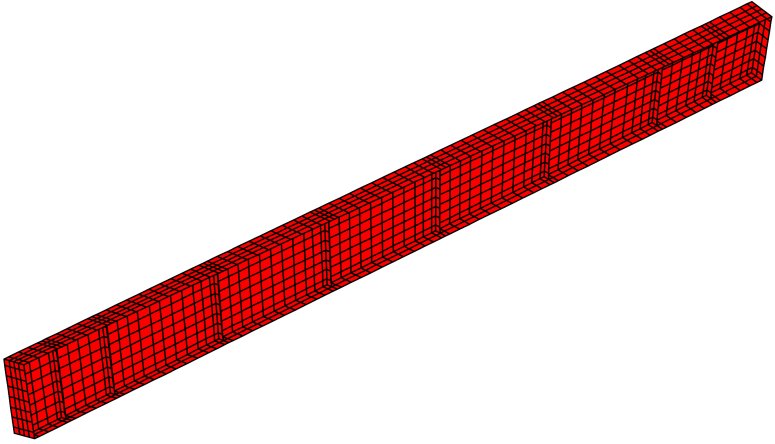
Bridge assessment using the BS5400 code permits making use of finite
element analysis to calculate effective lengths but does not make it an obvious
alternative to using standard code provisions. The draft version of Eurocode 3 Part 2 -
Bridges and Plated Structures explicitly states that eigenvalue analysis using finite
element methods can be performed to ascertain buckling characteristics of a structure.
This makes analysis software such as LUSAS Bridge an obvious alternative when
carrying out an assessment.
LUSAS Bridge provides a very practical and cost-effective way of
proving the integrity of all types of bridge structures that fail initial assessment to BS
5400 or indeed any other design code. It helps eliminate the need for otherwise
potentially costly strengthening, remedial works and traffic management.
Find out more
Other LUSAS Bridge case studies:
|